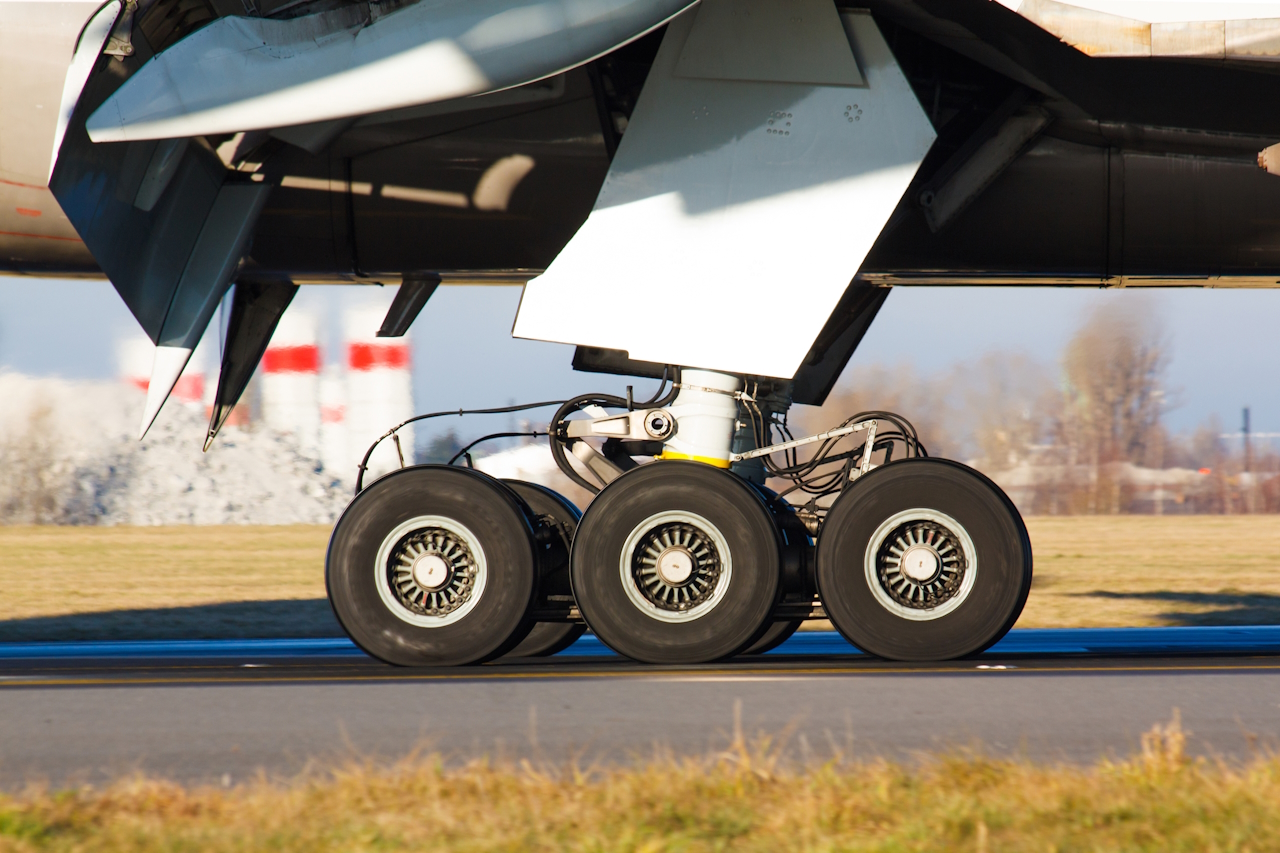
A combination of high strength, toughness, and fatigue resistance are the main requirements of the steels utilised for aircraft landing gear components. The steel should either be plated, or constructed of durable and robust stainless steel to withstand corrosion challenges.
By Dr. Gregory Vartanov, Advanced Materials Developing Corp., Canada
Precipitation hardening (PH) stainless steels are the best materials to meet the requirements of aircraft landing gears. There are several commercial high-strength PH stainless steels on the market. The most fitchered material is Custom465 steel alloy (Carpenter Technology Corp.) with a tensile strength < 1800 MPa, a fracture toughness of <95 MPa×m1/2, and corrosion resistance in salt spray test (1). It should be noted that all commercial PH stainless steels have tensile strength below 300M steel of >1950 MPa. The lower than 300M steel strength limits applications of PH stainless steels as the materials for high-stressed aerospace landing gear components.
A newly developed high-strength PH stainless steel alloy (PHSS alloy) combines tensile strength and fracture toughness higher than 300M steel. At the same time, it shows corrosion resistance in salt spray test per ASTM B-117 (5% NaCl solution, natural pH, and at 35°C). The high performance of PHSS alloy is achieved through precipitation of two different intermetallic phases that supply a tensile strength >1950 MPa and a fracture toughness >65 MPa×m1/2, while the concentrations of Cr>12%wt. and Mo>1%wt. in its solid solution provides sufficient corrosion resistance.
Description
PHSS alloy is a Fe-Cr-Ni-Ti-V-Mo composition which is mostly hardened by the precipitation of the following two nanometer-size intermetallic phases.
The binary intermetallic phase with chemical formula Ni3Ti has a formation temperature of >455°C, dissolution temperature of >980°C, ordered crystal structure with symbol D024 (D024 crystal structure), hexagonal close-packed unit cell (“hcp”), and a value of enthalpy of formation (“∆Hc”) of -38.07 kJ/mol.
The binary intermetallic phase with chemical formula Ni3V has a formation temperature of >455°C, dissolution temperature of >925°C, ordered crystal structure with symbol D022 (D022 crystal structure), face-centered cubic unit cell (fcc), and ∆Hc of -17.57 kJ/mol. Should be noted that intermetallic phase Ni2V with ∆Hc of -22.14 kJ/mol can be precipitated as well; therefore, the intermetallic phase NiXV, wherein 2≤X≤3 can be a part of PHSS alloy (2). Further, the NiXV intermetallic phase is designated as Ni3V.
The sufficient presence of alloying elements in the solid solution leads to significant transformations of the aforementioned binary phases. They can be transformed to complex intermetallic phases (complex phases) by substitution of Ni by one or more of Fe, Co, Cu, Mn and other transition metal; Ti and V by one or more of Hf, Zr, Ta, Nb, Mo, W; other transition metal. Transformations of the binary phases to the complex phases can lead to changes in their dissolution temperatures, and values of enthalpies of formation.
PHSS alloy is different from the commercial and newly developed by precipitation of two binary Ni3Ti and Ni3V phases and/or complex phases formed from the binary phases. Additionally, PHSS alloy can be hardened by precipitation of the binary Ni3Mo phase and Mo-rich phase. Premium ingots of PHSS alloy are melted by vacuum processes VIM-VAR or VIM-ESR, homogenise annealed at 1200-1260°C, and forged to bars with the preferable reduction ratio of 1:4 and more at 1200-1250°C.
Hardening of PHSS alloy consists of solution annealing at 980-1060°C for 1-2 hrs to dissolve undesirable precipitates, and rapid cooling, refrigerating at -40 to -70°C for 4-8 hrs and air warming; followed by two aging at 480-510°C for 4-8 hrs and air cooling.
The table shows the typical mechanical properties of lab scale ingots of PHSS alloy melted by VIM-VAR followed by hot forging and hardening. The mechanical properties of Custom 465 are shown for a comparison reason (6). Fatigue and stress corrosion cracking tests are underway.
The corrosion resistance of PHSS alloy is higher than the corrosion resistance of Custom 465 alloy due to higher concentrations of Cr and Ni.
The cost of production of PHSS alloy is similar to the cost of production of Custom 465 alloy, while the cost of raw materials is 5-10% higher.
The composition and method of manufacturing of PHSS alloy are protected by the US patent.
Typical mechanical properties of lab scale PHSS alloy ingots
UTS, MPa | YS, MPa | El, % | CVN, J | Kic, MPA×m(1/2) | |
PHSS | 1950 min | 1690 min | 8 min | 22 min | 65 min |
Custom | 1800 max | 1690 max | 12 max | 22 max | 95 max |
Conclusion
- New high-strength precipitation hardening stainless steel alloy is hardened by two different intermetallic phases
- The steel alloy possesses a combination of a tensile strength of >1950 MPa and a fracture toughness of >65 MPa×m1/2
- The steel alloy shows corrosion resistance in salt spray test per ASTM B-117
- The steel alloy is applicable for high-stressed aircraft landing gear components
References
- Benjamin T. Daymond, Nicolas Binot, Michael L. Schmidt, Steve Preston, Richard Collins, and Alan Shepherd “Development of Custom 465 Corrosion-Resisting Steel for Landing Gear Applications”, ASM International, published online February 29, 2016.
- Lei Zou, Cuiping Guo, Changrong Li, Zhenmin Du “Experimental investigation and thermodynamic modeling of the Ni–Ti–V system” Calphad, Volume 64, March 2019, Pages 97-114.
- H. Sugimura, Y. Kaneno, T. Takasugi “Alloying Behavior of Ni3M-Type Compounds with D0a Structure”, Materials Transactions, Vol. 52, No. 4 (2011) pp. 663 to 671.
- H. Sugimura, Y. Kaneno, T. Takasugi “Alloying Behavior of Ni3Nb, Ni3V and Ni3Ti compounds”, Materials Science Forum, Vol. 654-656 pp. 440- 443, June 2010.
- U.K. Viswanathan, G.K. Dey, and M.K. Asundi “Precipitation Hardening in 350 Grade Maraging Steel”, Metallurgical Transactions A, Volume 24A, November 1993-2429.
- CarTech® Custom 465® Stainless; Technical Datasheet, Carpenter Technology Corporation, Edition Date 6/27/2016.
About the author
Gregory Vartanov is Chief Engineer at Advanced Materials Development Corp., a Toronto-based company that develops new high-strength steels and alloys with a focus on aerospace and defense applications. Dr Vartanov holds an M.S. and a Ph.D. in materials science and metallurgy, as well as six US patents in high-strength steels and alloys. For more information: www.amdoncorp.com or email: info@amdoncorp.com