Q: Our team is considering hyper duplex for an upcoming chemical industry heat exchanger project, what do we need to consider when selecting welding filler material?
A: Duplex stainless steels (DSSs), with ferritic-austenitic microstructure, have an excellent combination of corrosion and mechanical properties. Since their development, they have been pushed towards higher contents of alloying elements, particularly chromium, nickel, and nitrogen, aiming for higher-performance applications. Typical composition and mechanical properties of different DSS are summarized in Table 1.
To rank duplex stainless steels, the Pitting Resistance Equivalent number (PRE) is used, where the higher the number, the higher the pitting resistance. There are different formulas among them, PRE based on nitrogen content (PREN) is normally used to rank DSSs: PREN = %Cr + (3.3.% Mo) + (16% N). Standard, Super, and Hyper DSSs have a PREN of 35-40, 40-45, and ≥ 45, respectively. This makes hyper duplex stainless steels (HDSSs) the highest corrosion resistance alloy among all DSS groups. From the view of mechanical properties, HDSSs have higher yield and ultimate tensile strength compared to the other grades. The unique alloy design provides high toughness values comparable with other DSS grades. Coupled with their excellent corrosion resistance, HDSS is the highest-performing grades among all DSSs.
Table 1. main alloying elements in weight percent and properties of some known DSS grades
Grade | Group | Cr | Ni | Mo | N | Co | PREN | YS (MPa) | UTS (MPa) |
2205 | Standard DSS | 22 | 5 | 3 | 0.2 | – | 35 | 485 | 680-880 |
2207 | Super DSS | 25 | 7 | 4 | 0.3 | – | 43 | 550 | 800-1000 |
SAF 2707 HD | HDSS | 27 | 7 | 5 | 0.4 | 1 | 48 | 700 | 920-1100 |
SAF 3107 HD | HDSS | 27 | 7 | 3.5 | 0.5 | – | 50 | ≥700 | ≥850 |
ESAB Exaton 27.7.5.L |
HDSS welding wire | 27 | 7 | 5 | 0.4 | 1 | 49 | 750 | 900 |
*Alloys contain Si and Mn as well as traces of other elements. Max carbon content is 0.03 wt.%.
Alloy design
The thermodynamic calculation, Figure 1a, shows that an equal fraction of ferrite and austenite may be achieved at temperatures around 1100 °C. Heat treatment or reheating below that temperature may result in the formation of detrimental phases such as sigma phase and nitride.
To compare the performance of SDSS and HDSS, the PREN values of ferrite and austenite calculated using Thermo-Calc software are shown in Figure 1. As may be seen at a temperature range of 1100-1200 °C, PREN of both ferrite and austenite is more than those for SDSS, exceeding 48. Thanks to its great alloy design, optimum PREN of ferrite and austenite is achieved when their content is almost equal. It should be noted that we used typical alloy composition for the calculations, and the PREN of ferrite and austenite might vary based on the actual composition.
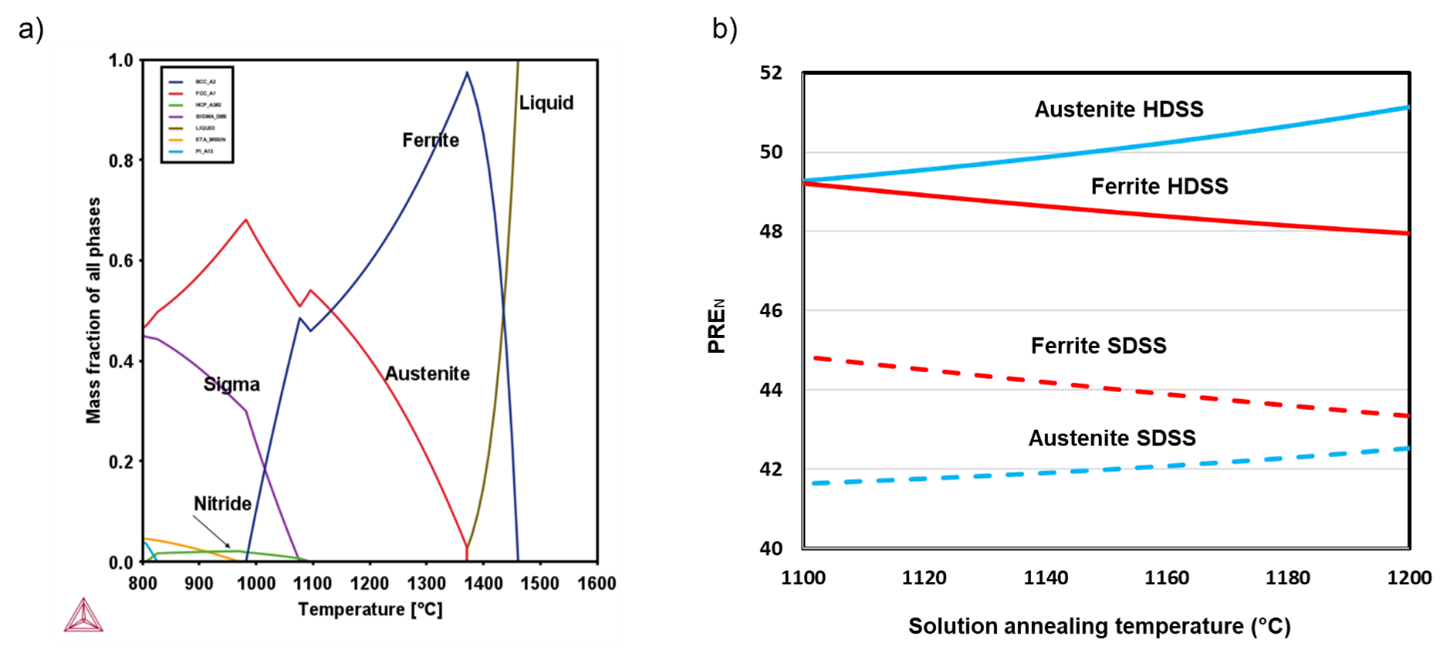
Welding filler metal
The unique alloying design of HDSSs requires highly engineered filler metal to deliver the required properties for different high-performance applications. Exaton 27.7.5.L has been designed to deliver high mechanical and corrosion resistance performance in complex welding thermal cycles. The typical microstructure of the root pass fabricated using this HDSS filler wire is shown in Figure 2. The weld shows a balanced fraction of ferrite and austenite, and no indication of fine secondary austenite clusters and detrimental intermetallic phases was found.
In addition to the welding of HDSS products, welding wires provide the opportunity to use HDSS in a wide range of applications. Weld overlays, root passes of super duplex stainless steel welds, and welding of 13% Cr stainless steels are a few applications that can locally enhance the performance of different components using HDSS welding wire. Some applications of HDSS welding wires will be explored in upcoming issues of Stainless Steel World.
Application
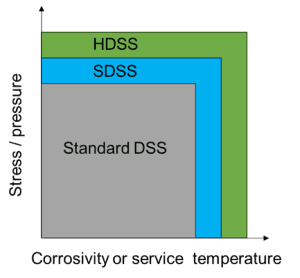
The schematic comparison of service temperature, corrosivity of environment, and stress/pressure level applied on the components for different duplex stainless steels is shown in Figure 3. Thanks to the high strength-to-weight ratio, as well as high critical pitting temperature, HDSS products are great candidates where a combination of high pressure, high temperature, and highly corrosive environment are present. This includes tropical seawater, components for chemical and petrochemical applications, and heat exchangers. The alloy is a great alternative to nickel alloys for the above-mentioned applications. To sum up, HDSS has a great potential to be used in highly corrosive and load-bearing conditions thanks to their excellent composition and microstructure design, making them sustainable choices in many different applications.
References
- Alleima product datasheets for different duplex stainless steel grades.
- ESAB product datasheet for Exaton 27.7.5.L
- Guocai Cha, Pasi Kangas, Hyper-Duplex Stainless Steels, How A New Generation of High-Alloy Stainless Steels Is Helping To Overcome Challenges In The Offshore Oil And Gas Industry, Sandvik white paper.
Meet the columnist
Dr Vahid A Hosseini
Dr Vahid A Hosseini joined ESAB in 2021 and is the manager of the Research Team at R&D Filler Metal, ESAB, Gothenburg. He received his doctoral degree related to Welding Metallurgy of Stainless Steels in 2018. Before joining ESAB, he worked as an assistant professor at University West, Sweden. His background is in welding metallurgy, working on processing-microstructure-properties relationships in welding and additive manufacturing of ferrous and non-ferrous alloys.
About this Tech Article
This tech article appeared in Stainless Steel World, June 2024 magazine. To read many more articles like these on an (almost) monthly basis, subscribe to our magazine (available in print and digital format) – SUBSCRIPTIONS TO OUR DIGITAL VERSION ARE NOW FREE.
Every week we share a new Featured Story with our Stainless Steel community. Join us and let’s share your Featured Story on Stainless Steel World online and in print.