Featured Story: Working with a myriad of heat exchangers
Management Summary
Located at Rotterdam in The Netherlands, Shell’s Pernis facilities form part of the largest refinery in Europe and one of the biggest in the world. They cover an area of more than 1000 football pitches and employ over 1900+ staff spread over 60 plants. Working there is Arjan Woerden, a materials and corrosion engineer who is charged with looking after the crude distillation units (including hydrotreating units), the platforming unit , and the hydro-conversion (hycon) unit. Heat Exchanger World met up with him to talk about his passion for his everyday working life and the challenges he faces in it.

Shell Pernis at night – a bundle of Christmas lights

Shell Pernis
Heat Exchangers at Pernis
At Shell’s fully-complex and integrated refinery in Rotterdam there are more than 1500 shell & tube heat exchangers and close to 900 airfin heat exchangers.
It is therefore not surprising to find that without them Shell would not be able to run its process units where they are used for process cooling and heating, and for heat integration.
Certainly, working with heat exchangers is not always simple as the challenges they often pose are multiple: two of the most prominent being fouling and corrosion. The fouling issues have much to do with the changing type of feedstocks that Shell Pernis processes.
“From a feedstock perspective,” says Mr. Woerden “the crudes we process today are no longer the easy ones of the past, which we would nowadays affectionately call ‘baby-feed’. Increasingly, they come from harsher and more corrosive environments and contain increasing amounts of hydrogen sulfide, sediment, acidic species, and scavenging chemicals. Moreover, for us as a company to survive nowadays, in an era of energy transition, as well as to stay ahead of the competition, it is imperative to be able to process every single crude the market can throw at you to maximize delivery to our bottom-line; or simply said: to make money. ”In addition to the corrosion that results from processing a wide variety of crudes, the brackish water from the river Nieuwe Maas, which is used as a coolant for the heat exchangers, also leads to considerable corrosion risks due to its salt level, and the sediment and marine biology (bacteria) it contains.

The Shell Pernis refinery covers an area of more than 1000 football pitches and employs more
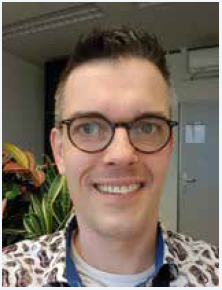
Arjan Woerden
“When all is said and done, there is little difference between a pipeline under pressure and an aircraft fuselage under pressure. The only difference is the materials used.”
Holding a Masters’ degree in Aerospace Engineering, Mr. Woerden majored at university in aerospace materials focusing on thermoplastic materials, fiber-metal laminates, and aluminium.
End Products
At Shell Pernis a whole scala of products are made, which can be grouped into oil products and base chemicals. Amongst others Shell Pernis produces bitumen, asphalt, gasoil, naphtha, kerosene, diesel, mogas, alkylate, platformate, LPG, propane and butane, and sulfur. Other, less common products for the general public, include CO2 for the greenhouse farmers in the area. “In effect,”” says Mr. Woerden “all base products that can be produced from crude oil are made in our plants at Pernis”.
Summing Up
Summing up Mr. Woerden had this to say: “What I always find particularly enjoyable about my job is that even though I am employed to be proactive and to insure that we avoid downtime with our assets, I always enjoy the surprise that every workday brings. I never know exactly what I will be doing. As such my job continues to challenge me on a daily basis. You have to be able to get up to speed very fast, particularly when you get a phone call from a unit to help them solve an issue. My job therefore combines daily problem-solving with the longer term goal to make all our production units work better, with minimum downtime, and with a very-low-to-non-existent incident rate. In Pernis we have units over fifty years old and we want to keep them running for many years to come.
This Featured Story is an abstract of the 4 page Featured Story in our Stainless Steel Magazine. If you want to read the full Featured Story and much more stories, subscribe to our print magazine.
Video Message
Jos Winsen, Vice President NL/DK and GM Pernis Shell
Shell Pernis, The Netherlands
“Every two weeks we share a new Featured Story with our Stainless Steel community. You can find here an abstract online and you can access the full story in our print magazine. Join us and let’s share your Featured Story also, on Stanless Steel World online and in print.”
– FEATURED STORY BY BRITTANI SCHROEDER
Editorial Manager KCI Media Group