Story by: Joanne McIntyre
Lincoln Raikes founded Global Stainless in 2004 to chase a very specific dream: to create perfect stainless steel spheres in a high mirror polish better than anyone else in the world. His success in achieving this dream means spheres, domes, bends, and other shapes are exported around the world from his workshop in New Zealand, destined for both artistic and industrial applications.
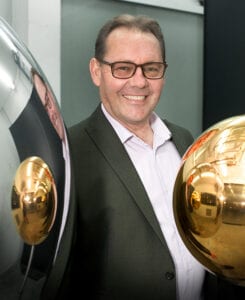
Global Stainless was founded in 2004 by Lincoln near the city of New Plymouth, New Zealand. Lincoln had started experimenting with spheres back in 1995 and patented his specialist double curve manufacturing process in 2000. For many years he had the aspiration of creating stainless steel balls with no weld shrinkage, leaving a seamless orb with a mirror-like finish.
“I had a vision of becoming the best stainless-steel fabricator of spheres in the world, and now we are. I saw how extremely labour-intensive conventional forming methods were in producing spheres and dreamt that there must be a better way. I started 25 years ago and discovered the fundamental method through very long hours and experimentation in the first year. It took over 20 years to perfect the method.”
At the same time, Lincolns team developed techniques for achieving an exceptionally highly polished surface far beyond a normal mirror-finish. The company is now exporting exceptionally highly polished curves and spheres around the world.
Combining art and industry
Lincoln’s company has two distinct entities, Global Stainless Artworks, which specialises in highly-polished stainless spheres and other shapes
for the most elite in the artworld;
and Global Stainless Industrial which produces vessel heads for the dairy, transport, and food industries. They also fabricate long radius bends for pipework and ducting. Their specialised manufacturing process allows Global Stainless to produce formed bends in a much larger diameter than had previously been available, and spheres in literally any diameter.
Tanks & pressure vessels
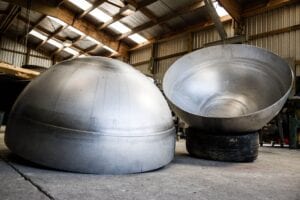
The Global Stainless Industrial team manufacture a range of different shaped vessel heads for tanks and pressure vessels in stainless steel, carbon steel and aluminium. The team specialises in fabricating smooth radius bends in any diameter and radius, and these are used for any application where smooth flow, lower back pressure and minimal product damage is essential. Examples of applications for these include milk powder processing, wine grape skins, beer grain mash, potato chip and fertiliser transportation.

“Our spheres, hemispheres (half sphere) and long radius bends have great potential for a wide range of industrial applications. Forming is performed post-welding to avoid any weld shrinkage or distortion in the finished product.”
Global Stainless now have a high demand for hemispherical domes which offer a lot smoother contour than conventionally made hemispheres which are typically made from inaccurately pressed plates and suffer weld shrinkage when assembled. “The smooth surface we offer allows a scraper agitator to glide across the whole surface which is perfect for avoiding burn-on of products often produced in the health, cosmetic, dairy and food industries as this makes them more hygienic and easier to clean.”
Pharmaceutical & space applications
Pharmaceutical & space applications
Lincoln and his team are keen to see the use of their spheres and domes expanded in industrial applications.
“We already polish to a standard which is far beyond anything required in the pharmaceutical industry. We can make a sphere or hemisphere (half ball) to any diameter and up to 12mm thick with pressure vessel certification and with weld seams 100% radiographed which means they are so versatile for use in steam sterilized pharmaceutical and cosmetic manufacturing vessels.”
“Another potential application is pressure vessels for rockets and aerospace applications. By stretching the steel, we increase the tensile strength, thereby increasing the strength of the vessel. The strength to weight ratio of our spheres is unparalleled. We’ve been approached by SpaceX and hope to cooperate with them in the future; our method to produce spherical fuel tanks produces a far superior product.”
The big breakthrough: Anish Kapoor
One of the company’s first significant breakthroughs was when London-based artist Anish Kapoor requested a sample sphere as he planned his sculpture ‘Tall Tree and the Eye’ which was commissioned by the Royal Academy in London in 2009. The resulting order for 74 spheres led to Global Stainless doubling its staff and beginning much larger scale manufacturing.

‘Tall Tree and the Eye’ stands 15 metres tall and resembles giant shiny bubbles emerging from the ground. The stainless steel spheres are designed to withstand wind and movement from potential earthquakes. The balls weighed 4 tonnes and the internal structure 7 tonnes. While being exhibited in London, the work was bought by South Korean clients; however, the Guggenheim Museum in Spain had booked it for an exhibition after the show in London,
so the South Koreans waited a year for their own replica to be fabricated. Meanwhile, Singapore clients asked Kapoor to produce a sculpture half the size, using only 28 spheres custom-built for their location. Anish Kapoor then commissioned a fourth, full-size model for Bill Gates business partner, the late Paul Allen, in southern France.
Genius in the genes
Global Stainless is very much a family business, with Lincoln’s four sons Bergen, Radcliffe, Wilbur and Chelton joining him on the workshop floor. “Their commitment is great – Bergen the second oldest of Lincolns seven sons is a natural engineering genius – and they are all extremely talented. Specialised work like this attracts like-minded folk; before we hire someone, we find out what their hobbies and passions are. If they’re doing engineering projects in their spare time, we know they will be a good fit.”
Experts in working with stainless
“Experience has shown that stainless steel grade 304 is ideal for our purposes due to its nickel content, and because as an austenitic steel it allows stretch forming. Grade 316 is a second choice as the molybdenum content causes early work hardening, and forming is slightly less desirable. We avoid martensitic grades as these have less elongation” explains Lincoln.
Consistently high-quality material is critical for success, explains Kerry Fowler General Manager at Global Stainless. We usually source material from Outokumpu or Aperam.

Unique farming technique

While Lincoln doesn’t want to give away too many secrets, he did provide some insights into his unique method for achieving a perfect sphere.
“We stretch-form the spheres after the weld seams are complete; this eliminates the chance of weld shrinkage and indentation. With the right welds we have found 300 series nickle-based alloys to have excellent stretching characteristics.”
“The beauty of what we are doing is that our method allows us to custom build spheres and bends to any diameter with incredible accuracy with plate up to 12mm”.
Polishing is carried by highly skilled artisan polishers who have at least three years of polishing experience.

“Our most ambitious project so far was a 3m diameter, 6 mm wall thickness sphere for a leading artist to exhibit in New York. The sphere also had two concave mirrors fitted into it. The polishing was true number 8 ultra-high mirror, and it was not possible to detect any weld seams in the finished product. On completion, it was flown to New York in a purpose-built, foam-lined protective crate made to an extremely high standard for the client.”
Every week we share a new Featured Story with our Stainless Steel community. Join us and let’s share your Featured Story on Stainless Steel World online and in print.
Featured Story by: James Chater
All images were taken before the COVID-19 pandemic, or in compliance with social distancing.