^ New facility – Chromeni Steels in Gujarat, India is one of the largest integrated stainless steel manufacturing sites in the world.
Article by Daniel Sweet
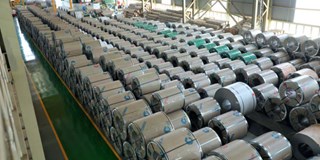
The story of Chromeni Steels begins with Chinese stainless steel manufacturer Tsingshan Industries and an invitation. Keen to live up to their corporate motto of “Dare to be the First,” Tsingshan began eyeing India as a potential site for investment several years ago. The first step for Tsingshan was to observe and strategize, which eventually led the stainless steel giant to seek out the top players in the Indian market. The choice was clear: the Shah family, with over 40 years of experience in Indian stainless steel, were ideal business partners.
An invitation to the Shahs led to a meeting in Shanghai in August 2016. From there, both parties took up planning in earnest, culminating with a Memorandum of Understanding in January 2017. Chromeni Steels would unite the scale and scope of the largest stainless steel producer in the world with five leading business houses of India, securing the company’s success in India and on the global market.
The unique, multi-national collaboration between Tsingshan and their Indian partners make Chromeni the biggest joint venture in the stainless steel industry. On the Indian front, Chromeni Steels consists of Sunrise Group, Suncity Group, JP ISCON, and VD Group.
Sunrise Group has a long history serving domestic and international stainless steel markets for the past four decades. Suncity Group brings 25 years of experience in stainless steel to Chromeni, while JP ISCON brings expertise in real estate development in Gujarat and Mumbai. Finally, the VD Group has been active in the diamond industry for a decade, with their most recent diversification being stainless steel.
Construction completed
As Mr. Pratik Shah explained in a recent interview, the first step to setting up Chromeni for production was to begin construction of a new facility. “The foundation stone for the facility, located in Mundra, in the Western state of Gujarat, India, was laid on January 23, 2018. In a record-setting 14 months, work on the facility was complete, and since August 2019, we have been up and running.”
Chromeni’s new facility—part of a USD 2 billion investment—ranks among “only a handful of stainless steel manufacturing plants that can accommodate melting, slab casting, and hot/cold rolling for coil production at one location. In fact, it’s the fourth largest facility with this capability in the world,” said Mr. Shah.
Chromeni leadership has a number of goals for the site. “Our targets stretch over five years. By the end of 2019, we expected an output of 1 million cold rolled coils. Happily, we met that goal.
By 2022 we are aiming for an additional 1 million cold rolled coils, and by 2025 our goal is to have produced 4 million hot rolled coils in mainly the 200 & 300 series. These are ambitious targets, but due to investment in the latest manufacturing equipment and techniques, we are confident that our goals can be met.”
Automation
Mr. Shah noted that “the facility is completely automated with the help of sophisticated software. The software enables every component of the system to synchronize. This is important for two reasons: it keeps the production line up to a high standard of productivity and a high standard of quality. With such high capacity—one line producing almost 1 million tons of stainless steel annually—standardizing and automation of the process is of the utmost importance.”
DRAP, 5 stand mill
Mr. Shah went on: “Chromeni’s production is quite unique. We have set up a DRAP (Direct Rolling Annealing Pickling) line in a 5-stand tandem mill, which is unlike anything else in the world. The production lead time is quick, completing the finishing process in minutes rather than the weeks required by conventional finishing techniques.”More detail on the DRAP line can be found in a feasibility study produced by Chromeni. That document reveals that the DRAP line is mainly used for “rolling, annealing, pickling and skin pass rolling in order to produce qualified cold rolled stainless steel coil fully and continuously.”
After the stainless steel enters and exits Chromeni’s 5-stand tandem mill, it undergoes solution heat treatment in the horizontal catenary annealing furnace. In the pickling section, the strip is pickled in a process of “neutral salt electrolysis + mixed acid pickling,” and the pickled strip enters the intermediate looper before coming to 2-h skin pass mill.
After skin pass rolling, the strip runs to the horizontal inspection section where both the top and bottom surface of the strip are inspected to determine if the strip needs to be dressed or even reprocessed. With the help of weld seam tracking system, the line slows down automatically when the weld seam reaches the exit section and the exit hydraulic shear cuts the strip at the point before or after the weld seam. At the final stage, the coil is unloaded from the tension reel and is prepared for storage.