NASA is utilising Crack Image Quality Indicators (CIQIs) to optimise X-ray part inspections and develop a rapid, cost-efficient crack verification technique.
Text & images by NASA

Innovators at NASA Johnson Space Centre have developed a modelling and manufacturing technique that generates unique verification tools that simulate metal cracks within X-ray setup part-testing geometries. The tooling specimens, such as the example shown with its manufactured circular crack, also enable verification of x-ray radiography sensitivity for crack detection inspection setups. Given the complications associated with crack detection via x-ray radiography, steps must be taken to ensure detection reliability. Thus, a demonstration of crack detection with a specific crack demonstration tool is performed to estimate the probability of detection (POD).
An ideal crack demonstration tool will match the alloy type, geometry, thickness, and expected crack morphology of the components to be tested. An inexpensive crack verification toolset that accurately represents crack-like discontinuities for various metal components would allow for reliable crack POD demonstrations while costing less and saving time over users having to generate their own fatigue crack specimens.
The technology
X-ray radiography is commonly used for the detection of cracks in metal parts such as those used in the aerospace industry. A typical application is for weld inspection where volumetric flaws such as pores, inclusions and flaws resulting in volumetric features such as suck-back, and under-cut are detected. The x-ray inspection of welds is also meant to detect crack-like or tight flaws and cracks that provide linear indications.
X-ray inspection reliability is based on POD of the desired minimum size cracks in suitable crack specimens. The demonstrated x-ray technique is then assumed to provide the same level of POD in actual part inspection. However, in many cases, the POD demonstration specimens and setup are not similar to that used for x-ray inspection of actual parts due to the lack of appropriate demonstration crack verification toolsets. The ideal demonstration toolset shall match the parts to be tested in alloy type, part geometry, thickness and expected crack morphology, target crack size, locations, and orientations. If a qualified CIQI tool is available at the time of part inspection, x-ray technique sensitivity for crack detection can be verified for the part inspection setup.
A CIQI toolset could provide simulated known crack sizes and have the same material and geometry for x-ray inspection to that of the actual part. Ideally, the appropriate crack specimen can be used to make a CIQI tool, but manufacturing specimens with cracks of controlled morphology and size for different x-ray applications with different material alloys and thicknesses may be impractical and cost prohibitive. Therefore, cheap CIQI toolsets with representative cracklike discontinuities may be desired by industry. The Crack Image Quality Indicator (CIQI) is a technology readiness level (TRL) 6 (system/sub-system model or prototype demonstrated in an operational environment). The innovation is now available for companies to license; note that NASA does not manufacture products itself for commercial sale.
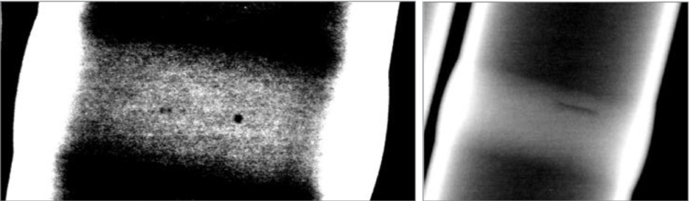
Benefits
- Characterises crack detection capabilities
- Enables development of crack detection requirements/standards
- Optimises X-ray radiography test setups
- Inexpensive to manufacture
- Use of standardised crack verification toolsets can save time
Applications
- Industrial x-ray radiography
- Aerospace manufacturing
- Gas and oil pipeline manufacturing
- Gas turbine manufacturing
- Prosthetic manufacturing
NASA is actively seeking licensees to commercialise this technology. For information, visit https://technology.nasa.gov/patent/MSC-TOPS-87
About this Tech Article
This tech article appeared in Stainless Steel World, April 2024 magazine. To read many more articles like these on an (almost) monthly basis, subscribe to our magazine (available in print and digital format) – SUBSCRIPTIONS TO OUR DIGITAL VERSION ARE NOW FREE.
Every week we share a new Featured Story with our Stainless Steel community. Join us and let’s share your Featured Story on Stainless Steel World online and in print.