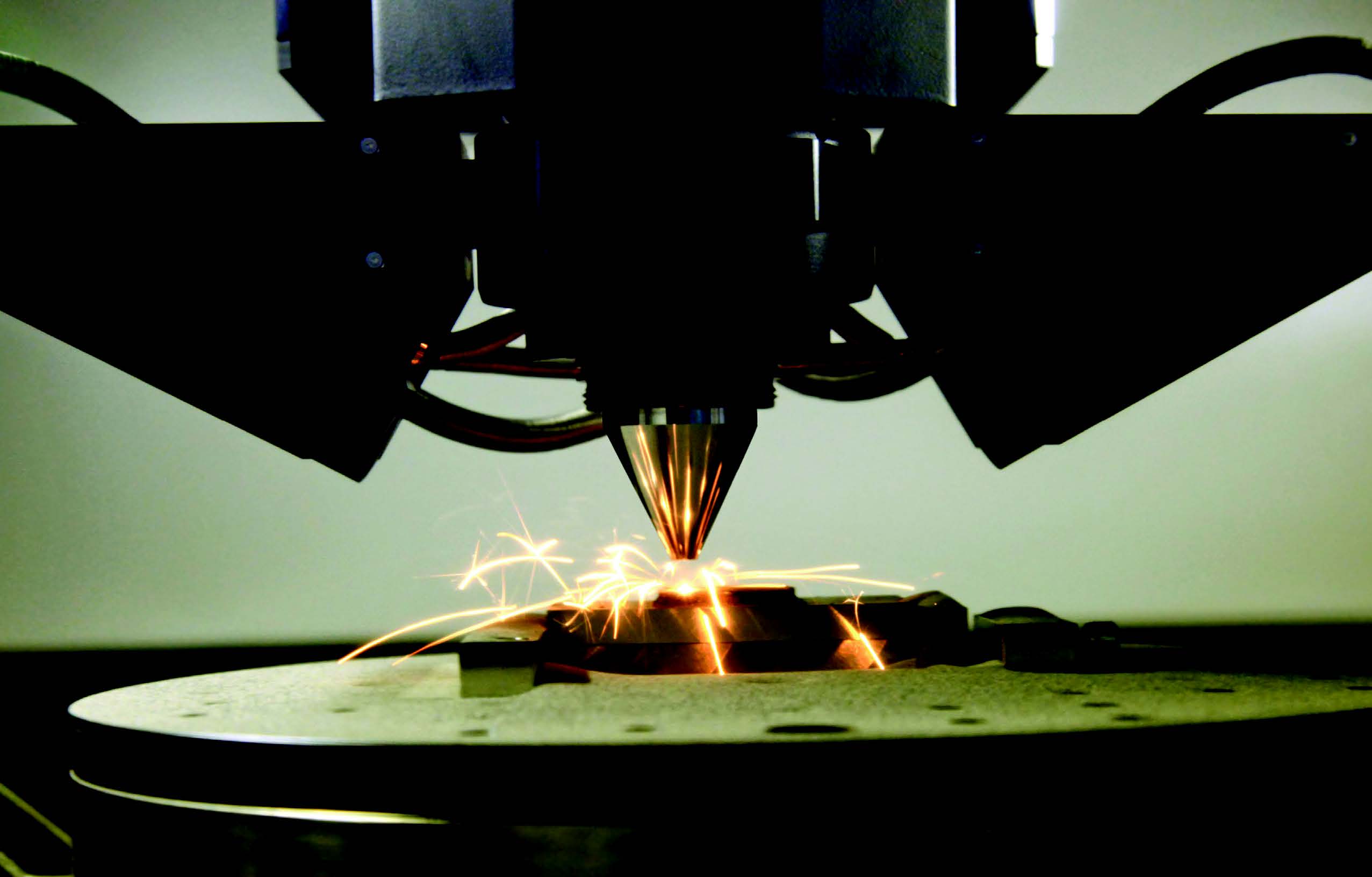
Stainless Steel World is proud to present a series of technical articles on additive manufacturing written by additive manufacturing expert Prof. Todd Palmer from PennsylvaniaState University. In this final article, he considers how the industry will continue to evolve.
By T.A. Palmer (a,b, a) Department of Materials Science and Engineering and (b) Department of Engineering Science and Mechanics, The Pennsylvania State University, USA
Additive Manufacturing (AM) is touted as an innovative manufacturing process that will lead to a revolution in manufacturing. In reality, it is still a niche manufacturing route with a rather small market size compared to traditional metals production and manufacturing industries. Although it has much promise, it will not be widely adopted until fundamental materials issues arising, in part, from insufficient understanding of process-structure-property relationships are resolved. At a practical level, AM processing suffers from large uncertainties in material properties and wide variability in product characteristics. Therefore much of the focus, particularly within academia, is on designing new alloys optimized for AM processing using machine learning and other advanced computational methods. The timeframe for developing, testing, and qualifying new alloys using conventional alloy development approaches has traditionally taken more than a decade to complete. Machine learning and related computational methods will likely shorten these cycles, but the validation testing required to qualify a new alloy system will remain far too long to make this approach a viable option in the short or even medium term. A more realistic approach would be to take advantage of these same advanced computational and characterization methodologies to develop tools that can predict the response of different combinations of compositions within allowable alloy specifications to post-processing operations. More consistent properties can be achieved by applying thermal heat treatments, hot isostatic pressing, or other thermo-mechanical processing routes. However, such an approach will require flexibility and new techniques that will allow rapid, real-time adaptation of processing parameters to accommodate variability in incoming materials.
Importance of materials in AM
The latest stage in the development of AM technologies started in the early 2010s with a surge in machine development that has continued unabated. Much of this growth can be traced to advances in technologies in the internal mechanics of the AM machines. For example, the current generation of lasers, motion control systems, robotics, and computational resources are vastly superior compared to when many of these technologies were first envisioned. Explosive growth in motion control systems and articulating robotics has expanded the size envelopes for AM processes. These now range from the micron-scale to full-scale vehicles and structures while maintaining high dimensional precision and tolerance levels.

The materials used as the primary AM feedstocks have not evolved at the same rate. Much of this lag in materials development can be traced to the origins of the technology. Even though AM processing is rather unique in its combination of materials processing and component fabrication, materials have largely been considered secondary to the components being produced, and selected based primarily on their availability in powder form. This lack of interest in the materials drove many early users to focus solely on commercially available alloys and feedstock forms to use in the processes. Stainless steels have been popular since the inception of the technology. Common austenitic and precipitation hardened (PH) grades like 316L and 17-4 PH, dominated early work and remain in common use as they are widely available in the gas atomized form, owing to their use in plasma transfer arc (PTA) and laser cladding applications.
Even though these alloy systems are treated as commodity products, they are actually complex multi-component alloys developed over decades of testing and investigation. Their combinations of alloying elements were optimized to undergo a series of highly controlled thermo-mechanical and heat treatment steps to consistently produce specific microstructures and properties. During AM processing, however, these material systems are subjected to conditions far removed from the tightly controlled thermo-mechanical treatments. For example, during fusion-based processes, such as powder bed fusion (PBF) and directed energy deposition (DED), fine spherical powders or wires are deposited in a layer-by-layer fashion, producing a complex series of rapid heating, melting, solidification, and cooling cycles1.
Depending on the energy source (i.e. arcs, lasers, and electron beams), the rapid heating and cooling experienced as the subsequent passes are deposited can produce a range of different solidification structures and microstructures. Significant alloying element segregation can then lead to the formation of non-equilibrium phases typically not encountered in the corresponding wrought alloy condition2. It should then come as no surprise that the microstructures and properties observed in AM processed materials are very different than those in more traditional wrought or cast alloy systems. These differences and the role that these different microstructures play on the resulting properties of austenitic, duplex, and PH stainless steel grades as well as the similarities with structures formed during fusion welding processes, have been addressed in the previous articles in this series3-6 . Given these similarities in AM and welded structures, it is widely accepted that alloys used in fusion-based AM processes must display good weldability, which typically refers to the propensity of the alloy to suffer from typical weld defects, such as solidification and solid-state cracking. In addition to the critical role of alloy compositions, the form of these feedstock materials also plays a major role in determining the final properties of the AM fabricated components. For PBF and DED AM processes, the feedstocks are primarily spherical pre-alloyed gas atomized powders, along with a growing use of wires in wire arc additive manufacturing (WAAM) processes. There are several advantages to using powders as the feedstock material when building a component in the layer-by-layer manner characteristic of AM processing. Their use offers the flexibility to easily mix different powders to create custom compositions or to vary the material composition during processing to fabricate high-performance, functionally graded materials (FGM)7.
While considered a separate issue in most cases, the properties of the powder particles and their rheological performance are rather intimately tied with the composition and need to be considered when specifying powders. In most cases, traditional measurements of powder properties are limited to defining general particle characteristics, such as the particle size distribution, apparent and tap densities, and flow rates. Most of these tests, though, were developed for traditional powder metallurgy applications, in which a mold is filled with a specified amount of powder. AM processing subjects the powders to many different conditions, which vary between PBF and DED processing routes. Rheological tools designed to test the behavior of powders in conditions more representative of those present in PBF and DED processes are being investigated. However, the general knowledge and understanding of how to define the most applicable measurements are still largely undefined and not mature enough for large scale application or standardization8-9.
Are new materials needed?
The specification and selection of materials in AM processing has been primarily based upon the use of standards designed for wrought products. This approach was both necessary and convenient since there were no existing standards for manufacturers to draw upon. However, it has limited the number of alloy systems available for AM processing and led to the inability to produce consistent material properties across various AM processes. In response to these issues, significant interest has grown in pursuing the development of new alloys designed specifically for AM. While this path forward seems logical, the approach to developing new alloys for a new process is not straightforward. It will require many fundamental scientific, technical, and economic choices before rushing into any large scale alloy development effort.
It is probably best to start with a fundamental question: How does one develop an alloy specifically for AM processing? Using a more traditional materials design methodology, the primary starting point is to select a baseline material system, such as titanium, nickel, or iron for stainless steel, to meet a set of performance criteria for a given application space. Much like existing commercial alloys, these candidate alloys will be dilute alloy solutions, with a dominant solvent element and the addition of small levels of solute alloying elements.
The selection of these additional alloying elements is based on the governing process-structure-property relationships for the alloying element combinations. As a professor, I make these relationships the foundation of every class I teach, from introductory ones taught to undergraduates through advanced materials classes for PhD-level students. In the development of current wrought alloys, highly controlled thermo-mechanical processes are used to produce specific microstructural features, whether it be uniformly distributed secondary phases or specific grain sizes. While this approach is time-tested and produces alloys that can produce highly repeatable microstructures and properties, an extended time of up to ten years or more is typically required.
However, AM processing routes are characterized by conditions far different from those utilized during wrought processing. They introduce additional complexity through many variables, including processing conditions, materials composition, and feedstock characteristics. Consequently, a robust understanding of the complex interplay among these variables and others that might not be immediately recognized is necessary for the alloy development process and tailoring the alloying element compositions to ill-defined and variable manufacturing routes. Such inherent complexity and a large number of variables can make traditional approaches to alloy development rather intractable, thus leading to the investigation of new methodologies for developing new alloy systems.
Developing AM specific alloys

The development of these AM specific alloy systems is an attractive topic for the academic community, with a particular emphasis on the use of modern computational tools, with an emphasis on the use of machine learning10. When combined with combinatorial material development approaches, many alloying element combinations can be evaluated rapidly and at a level of detail not possible through traditional methodologies. Machine learning can provide a means for identifying interactions or relationships between these various alloying elements under AM processing conditions, also not possible through conventional techniques. It is important to note, however, that many of these approaches have not been widely tested and are still really at their initial stages of development. Applying them immediately to the complex AM processing route represents a major challenge to overcome, while simultaneously trying to undertake the rather arduous task of validating and producing new alloys.
While the development of new alloys is critical for the long-term viability of AM processing, there are practical implications of focusing solely on this route, particularly in the short term. As with the existing alloys, standards will need to be developed for these new alloying element compositions, which will require the gathering of significant property data. Even with advanced computational tools, significant material testing over a wide range of processing conditions will be needed. Much of this work will support the quantification of uncertainty in the material properties across different manufacturers and allowable composition limits needed to develop design allowable properties similar to those in wrought materials. This work will be labour-intensive and time-consuming, and is not possible in the near term. It also doesn’t address the effect of new alloy compositions on powder particle characteristics and rheological behaviors that impact the AM processes in largely unknown ways.
In the shorter term, it will be a much more efficient use of time and resources to concentrate on existing alloy systems. There are some benefits to this approach. For example, these existing alloy systems are already well characterized in the powder, wrought, and welded forms, particularly for common austenitic stainless steels. Using the knowledge base in welding as an example, there are general rules of thumb and existing empirical tools that can be used to refine the allowable ranges of selected alloying element compositions. By refining selected alloying element compositions, such as Cr, Ni, Mo, and N, the phases formed and microstructures can be more closely controlled. These tools are also supported by current work that is directed at characterizing the process-structure-property relationships more likely that existing alloy element compositions can be refined to address changes in processing conditions and produce more consistent microstructures and properties.
Post-processing

When dealing with AM processed materials, much effort has been directed at understanding and characterizing the as-deposited condition. However, these materials can also be post-processed using more conventional heat treatment or hot isostatic pressing (HIP). While HIP post-processing is typically directed at removing or healing process-related defects resulting from lack of fusion between passes and layers, keyhole collapse porosity, or gas porosity, it can also be used like conventional heat treatments to manipulate microstructures11,12. Given the variability in the as-deposited microstructures, the use of these post-processing techniques represents a means for minimizing the inherent uncertainty in the resulting properties.
Post-processing operations, however, must also have built-in flexibility and be able to adapt the heat treatment process conditions to accommodate the different starting microstructures. Such flexibility, however, will require the development of tools capable of predicting specific properties in the as-deposited microstructures and their corresponding response to the heat treatments. The best starting point would use the starting composition and processing conditions as input for tools which can predict how the microstructures and properties will evolve during post-processing.
The path forward
New technologies, such as electric and hypersonic vehicles and renewable energy, will require alloys and material combinations capable of meeting higher performance requirements while also utilizing more sustainable processing routes. With this increasing emphasis on sustainability, the integration of recycling and reuse into product and material designs will also stretch current material capabilities and require more efficient processing routes. AM processing represents a pathway for enabling these new technologies and designs, but AM materials have not been optimized to fully exploit AM processing routes. While the introduction of new materials to the broad AM industry is expected to drive further innovation and shape the future competitiveness of US advanced manufacturing, current limitations in knowledge will constrain efforts to efficiently explore and develop next-generation materials.
For the wider implementation of AM processing to become a reality, tools that allow for an increasingly flexible and adaptable manufacturing base envisioned by Industry 4.0 proponents will be needed. Although many applied R&D efforts to advance the state of AM technologies are underway, successful materials innovation will require an alignment of efforts throughout the AM community. These include digital tools capable of adapting to rapid changes in processing parameters and incoming materials. The advanced manufacturing of metals will be more flexible and adaptable than traditional processing routes, which rely on fixed parameter spaces to improve process control13.
By coupling focused fundamental materials research, simultaneous design and manufacture is an appropriate path for exploring new materials for AM and knowledge gaps can be addressed directly and as part of the larger systems. These activities are organized into four strategic thrusts driven by end-user needs and designed to result in new and improved applications for AM materials:
- Integrated design, which encompasses all other thrusts into design tools for new AM materials
- Process-structure-property relationships, the cornerstone of material and process development
- Part and feedstock testing, which is needed to build the data required to design new materials and predict performance
- Process analytics to better understand and measure the effect of processes on AM materials
The sophisticated nature of AM processing carries an intrinsically large number of variables, including processing conditions, materials composition, and feedstock characteristics. Consequently, a robust understanding of the complex interplay among these variables and others is necessary for determining feasible manufacturing routes that demonstrate the value of new AM materials in end-use applications. Fundamental welding knowledge will be a key component in the design and eventual implementation of new materials; the lack of traditional geometric and processing constraints prevalent in the study of AM processing will introduce new challenges.
References
1 | T. DebRoy, H.L. Wei, J.S. Zuback, T. Mukherjee, J.W. Elmer, J.O. Milewski, A.M. Beese, A. Wilson-Heid, A. De, W. Zhang, Additive manufacturingof metallic components – Process,structure and properties, Prog. Mater.Sci. 92 (2018) 112–224. https://doi.org/10.1016/j.pmatsci.2017.10.001.. |
2 | J.S. Zuback, A.D. Iams, F. Zhang, L.A. Giannuzzi, T.A. Palmer, Stable nitride precipitation in additively manufactured nickel superalloys, J. Alloys Compd. 910 (2022) 164918. https://doi.org/10.1016/j.jallcom.2022.164918. |
3 | T.A. Palmer, Challenges and opportunities in the additive manufacturing of stainless steels, (2022) 48–50. |
4 | T.A. Palmer, Challenges and opportunities in the additive manufacturing of stainless steels. Part 2-Austenitic Stainless Steels, (2022) 34–37. |
5 | T.A. Palmer, Challenges and opportunities in the additive manufacturing of stainless steels. Part 3-Duplex Stainless Steels, (2022) 31–35. |
6 | T.A. Palmer, Challenges and opportunities in the additive manufacturing of stainless steels. Part 4-Precipitation Hardenable Martensitic Stainless Steels, (2022) 35–38. |
7 | J.S. Zuback, T.A. Palmer, T. DebRoy, Additive manufacturing of functionally graded transition joints between ferritic and austenitic alloys, J. Alloys Compd. 770 (2019). https://doi.org/10.1016/j.jallcom.2018.08.197. |
8 | A.D. Iams, M.Z. Gao, A. Shetty, T.A. Palmer, Influence of particle size on powder rheology and effects on mass flow during directed energy deposition additive manufacturing, Powder Technol. 396 (2022) 316–326. https://doi.org/10.1016/j.powtec.2021.10.059. |
9 | MZ. Gao, B. Ludwig, T.A. Palmer, Impact of atomization gas on characteristics of austenitic stainless steel powder feedstocks for additive manufacturing, Powder Technol. 383 (2021). https://doi.org/10.1016/j.powtec.2020.12.005. |
10 | A. Bandyopadhyay, KD. Traxel, M. Lang, M. Juhasz, N. Eliaz, S. Bose, Alloy design via additive manufacturing: Advantages, challenges, applications and perspectives, Mater. Today. 52 (2022) 207–224. https://doi.org/10.1016/j.mattod.2021.11.026. |
11 | M.C. Brennan, J.S. Keist, T.A. Palmer, Defects in Metal Additive Manufacturing Processes, J. Mater. Eng. Perform. 30 (2021) 4808–4818. https://doi.org/10.1007/s11665-021-05919-6. |
12 | J.S. Keist, S. Nayir, T.A. Palmer, Impact of hot isostatic pressing on the mechanical and microstructural properties of additively manufactured Ti–6Al–4V fabricated using directed energy deposition, Mater. Sci. Eng. A. (2020) 139454. https://doi.org/10.1016/j.msea.2020.139454. |
13 | T.A. Palmer, Materials Challenges in the Additive Manufacturing of Metals, Weld. J. 99 (2020) 31–35. |