A new autonomous system using both vision technology and industrial robotics automatically performs trimming and sampling in wire rod rolling mills. Developed by AIC Group, it operates without human intervention to improve accuracy and provide a safer working environment.
By Jens Nylander, Automazioni Industriali Capitanio Srl
When rolling wire in a long product rolling mill, the head and tail is usually of inferior quality due to production-related reasons such as uncooled front ends or uneven cooling on the conveyor. The ends are removed in a process referred to as coil trimming, typically within the confines of the coil-handling system. The most common method uses a system where the coil rests on the horizontal load-carrying member of a C-hook supported by an overhead conveyor structure. When the coil arrives at the manual trimming station, the front and back ends can be quite tangled, requiring untangling by the operator. The operator identifies, separates, cuts and removes pieces of the wire, ranging from a short sample to several loops from the exposed end of a coil. This activity creates a very poor work environment and is a frequent source of injuries to the operator. There is also a negative impact on yield and product quality as each operator may interpret and implement the static trimming instruction differently. AIC Group developed a patent-pending robotic system which eliminates manual trimming and cuts the wire with accuracy and repeatability, thereby reducing waste.
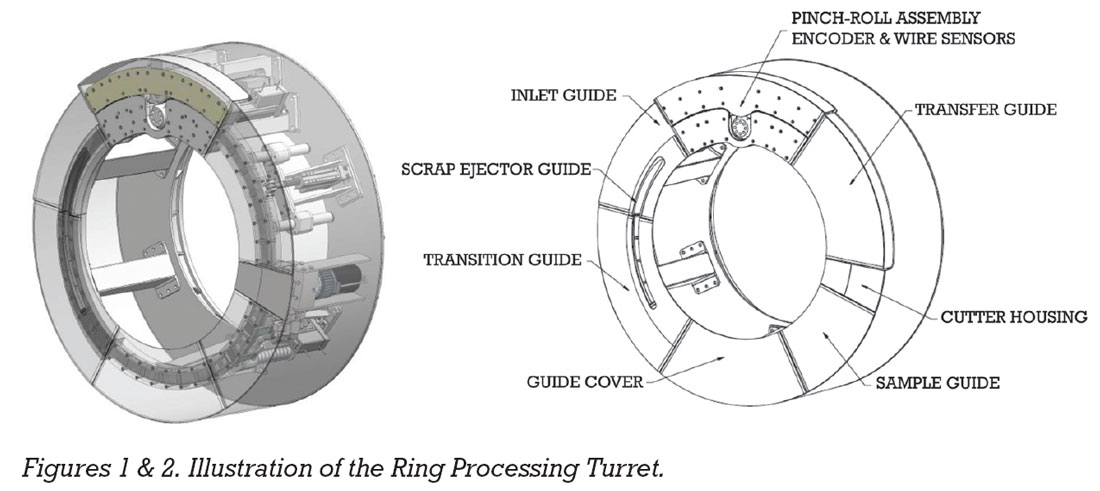

Robotic solution
The most obvious solution would be replacing human operators with robotic arms supported by a vision system to count loops. However, this approach would not add value to the process as it would continue the flaws and limitations of the manual process.
The solution was inspired by the process of forming the wire loop in the rolling mill laying-head. After being rolled into a straight round wire at a very high axial velocity, the wire enters the straight section of the laying-head pipe. When it exits the curved section on the other side of the pipe, it has the shape of a continuous helical loop.
The new method passes the looped wire through a similarly-shaped guide, thereby containing it without the risk of damaging the surface or shape of the finished wire. A wire feeding pinch-roll ensures a relative movement between the guide and the wire. The system automatically finds the end of the loop and then pushes it into the guide. A cutting device is placed at a specific distance from the pinch-roll.
All these movements require that the wire moves in a circular manner relative to the guide, both clockwise and counter-clockwise. Rather than rotating the entire coil, the guide turns while the coil remains stationary, creating order in the often tangled and unruly first few coil rings. The trim-cut occurs at the exact location and is highly repeatable. These developments ultimately led to the TRIMBOT. Its patent-pending Ring Processing Turret (Figure 1) is essentially a circular guide shaped to match the natural form of the coiled wire (Figure 2). Distributed along the circular guide are an advanced pinch-roll assembly, several sensors, guide segments and a cutting device. The Ring Processing Turret is mounted on a slewing ring bolted to the main trolley; a gear motor on the same trolley rotates the turret.
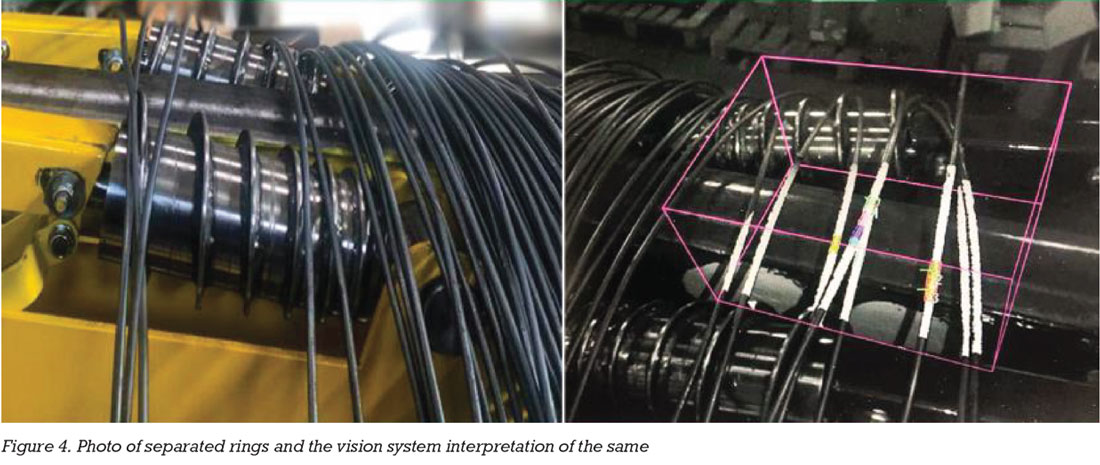
The Ring Processing Turret is able to:
• Receive a ring from the coil and bring it into the pinch-roll assembly.
• Rotate clockwise when facing the ring processing turret towards the end of the coiled wire.
• Locate the end of the coiled wire and stop.
• Rotate counter-clockwise away from the located end while measuring the exact position to make the trim-cut.
• Locate the trim-cut position, then cut.
• Rotate counter-clockwise away from the located end while measuring the exact position to make the sample cut.
• Locate the sample cut position, then cut.
• Eject the trimmed rings to be discarded.
• Eject the sample wire for testing.
The process works regardless of how the coil is oriented.
Robotic arm & vision system
A ring transfer and separation system (Figure 3) supports the interaction between the coil and the Ring Processing Turret. It pulls the forwardmost rings from the exposed end of the C-hook towards the turret while spreading them to create additional separation. An advanced vision system (Figure 4) takes a photo of the loops and selects which wire to pick based on an advanced image analysis algorithm. Having made the selection, a robotic arm collects and places the loop segment into the pinch roll of the ring processing turret. After the ring processing turret has performed its trimming and sampling sequence, the robotic arm collects and discharges the trimmed rings. If a sample is required, a separate sample guide extends to expose the sample to the robotic arm, which places it in the sample tray.
Benefits
The TRIMBOT is designed to be installed in front of an existing C-hook on any mill floor. The system is very compact, requiring approximately 10 m2 of floor space, while a safe work area with both sample and scrap collection will need 25-30 m2.
AIC’s ambition was to create a system that would pay for itself within 12 to 24 months, depending on production rate and product mix. The immediate cost savings originate from eliminating salaries and benefits to manual operators, but almost as significant are the gains in yield and cost reductions associated with scrap handling and processing.
For example, a manual ring-counting trimming process regularly trims one extra ring from both the head and the tail. By assuming a 2-ton coil with a wire diameter of Ø10 mm and an annual production of 200,000 tons, removing two extra rings on each coil amounts to the removal of 1.3 kg of the excess prime product. This equates to discarding 260 tons of prime product every year.
The TRIMBOT also introduces dynamic functionalities. For instance, the length of wire to be trimmed in manual operations is calculated based on a ‘nominal’ rolling speed for each diameter and steel quality. However, the actual speed may change from billet to billet throughout a rolling campaign. The TRIMBOT calculates the length of wire to be trimmed for each coil based on production data and product tracking information provided by the rolling mill to the TRIMBOT control system.
Conclusions
The electrical TRIMBOT fits almost any existing coil handling system with minimum disturbance to existing sites and allows a level of accuracy not possible on a ‘ring-counting’ trimming method. The process reaches a trimming accuracy of +/- 5 mm under certain conditions. It adjusts the trimming position based on the dynamic variations in the rolling process for each coil, reducing waste and yield losses.