Today’s market is increasingly driven by strong trends toward waste minimisation and the adoption of processes that support the principles of the circular economy. This article provides an overview of various technologies used to regenerate pickling solutions, including methods for recovering dissolved metals and recycling rinse water.
By Marco Zavattoni, Condoroil
During the production and transformation of stainless steel, oxides generated during the hot processes must be removed using specifi c pickling solutions. In particular, the main acids mix used today are: Chemical pickling: Sulfuric + hydrofluoric acids, or nitic + hydrofluoric acids Electrolytic pickling: Sulfuric acid (corrosive), or organic acids (irritant)
Acid regeneration
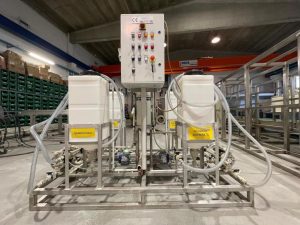
When properly used, regeneration technologies can achieve signifi cant targets, allowing a speedy return on investment, including:
- Steady and optimal pickling results
- Increase in the production capacity
- Reduced acid consumption
- Reduced waste treatment costs
- Reduced manpower in the handling of hazardous substances
- Recovery, in some cases, of secondary raw materials
Considering the regeneration of the pickling solution used for stainless steel treatment, two main factors to consider are:
- For the pickling of stainless steel –excluding the electrolytic solutions – the acids are costly and diffi cult to treat in the wastewater treatment (WWT) plant.
- The pickling activity, when considering the traditional nitro-hydrofluoric mix, varies signifi cantly with the concentration of the dissolved metals.
Both these characteristics justify an investment in a regeneration unit, even if only a fraction of the used acid is recovered. The most commonly used and widespread recovery technology utilises particular acid retardation resins able to separate the free acids that are recovered in the bath from the metal salts that are discharged (Figure 1). With fast and short elution* steps, the process can continuously drain the dissolved metals and avoid wasting reusable acids, using little energy.
Five step cycle
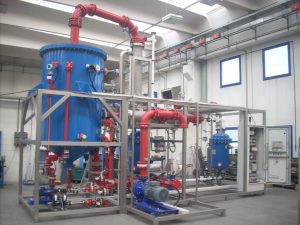
The complete regeneration cycle consists of five steps, two of which are the core of the separation process. Similar results can be obtained by utilising Diffusion Dialysis. This process allows for the recovery of free acids using a permeable ion exchange membrane, which prevents the permeation of metal salts that are then discharged into the WWT, as illustrated in Figure 2.
Each technology supplier has their own specific design for the separation modules and pre-treatment process.
An efficient pre-treatment process is the key to a reliable unit. The resin bed is very tightly sealed to reduce, as far as possible, any dead volumes which would reduce efficiency. The same considerations must be taken into account when considering Diffusion Dialysis technology, where the small channels can be easily clogged by fine oxides dispersed in the solution.
Although acid retardation and Diffusion Dialysis are the most used processes, in some specific cases, evaporative and hydro-pyrolysis technologies may be the best choice.
Using an evaporative unit (Figure 3), it is possible to recover, by distillation, free volatile acids such as hydrofluoric and nitric acids. If necessary, it is also possible to recover salified acids by adding concentrated sulfuric acid. With this addition, 100% of nitric and hydrofluoric acids are recovered. The waste residuals must be centrifuged to separate the metal sulphates on one side and recoverable sulfuric acid on the other (Figure 3).
By using a hydro-pyrolytic unit, it is possible to recover 100% of the hydrofluoric and nitric acids, producing metal oxides ready for use in metal recovery processes (Figure 4).
From a circular economy perspective, this is the best solution for recovering every component present in the waste stream.
Currently, the main reasons limiting the widespread adoption of this technology are the costs and the difficulty in treating nitric-free solutions due to the presence of sulfuric acid.
Oxidising regeneration
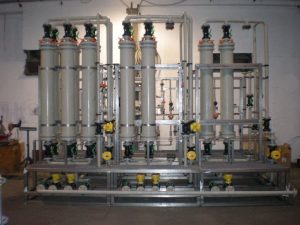
Another peculiarity of stainless steel is the requirement for an oxidising medium to perform the pickling operation. In particular, the oxidiser is nitric acid in traditional acid mixtures and trivalent iron in nitric-free solutions.
The pickling reactions that consume the oxidisers are the following:
2Fe3 + Fe° → 3Fe2+ Nitric free solution HNO3 + Fe° → Fe3+ + HNO2 → Fe3+ + NOx Traditional mix
The simplest way to regenerate the consumed oxidiser is to add hydrogen peroxide to the bath:
2Fe2+ H2O2 + 2H+ → 2Fe3+ + 2H2O
HNO2 + H2O2 → HNO3 + H2O
If the consumption of the hydrogen peroxide becomes too high, it is possible, with a catalytic oxidation unit, to use the cheaper oxygen according to the following reactions:
It is worth noting that both reoxidising products—hydrogen peroxide and oxygen—allow the recovery of nitric acid while simultaneously reducing NOx emissions to below 100 ppm.
The catalyst is necessary to reduce the activation energy barrier of the oxygen molecule’s double bond.
Water recycling
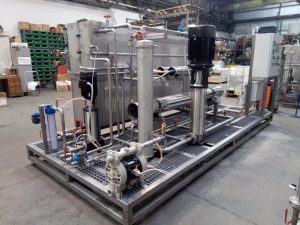
To provide a comprehensive overview of the recovery technologies used in stainless steel pickling, it is worth mentioning the possibility of recycling the water used for rinsing, with the goal of achieving zero discharge.
Generally speaking, the most efficient way to recycle water without producing additional waste for disposal is to purify the rinsing solution through the reconcentration of the drained pickling solution.
Two main technologies are used for reconcentration: reverse osmosis, which can treat large volumes of water at low investment and management costs, and evaporation, which can reach higher salt concentrations.
Depending on the specific case and, primarily, the number of rinsing stages, it is possible to use either one or both technologies simultaneously (Figure 5).
Metal recovery
The rising cost of disposing of waste sludge produced during the neutralisation of metal salt solutions discharged by acid regeneration processes (excluding hydro pyrolysis) combined with stricter requirements for discharged water quality (e.g., the new BAT regulation**) makes the use of an electrodialysis unit increasingly cost-effective.
This technology enables the recovery of both dissolved metals in metallic form and salified acids from the waste stream (Figure 6).
Conclusion
With the advancement of waste minimisation technologies, it is now possible to utilise nearly all of the dosed pickling acids and operate with zero water discharge at a cost comparable to, or even lower than, that of traditional chemical treatment units.
With special thanks from the environment!
Notes
* Elution is the process of recovering adsorbates and regenerating adsorbents by using desorbing agents, such as saline solutions or alkalis, based on their desorption efficiency and economic and environmental considerations. From: Chemical Engineering Journal, 2020.
** BAT regulation – https://eur-lex.europa.eu/legal-content/EN/TXT/?uri=CELEX%3A32022D2110
About this Tech Article
Appearing in the May 2025 issue of Stainless Steel World Magazine, this technical article is just one of many insightful articles we publish. Subscribe today to receive 10 issues a year, available monthly in print and digital formats. – SUBSCRIPTIONS TO OUR DIGITAL VERSION ARE NOW FREE.
Every week we share a new technical articles with our Stainless Steel community. Join us and let’s share your technical articles on Stainless Steel World online and in print.