Like any other major industry, the stainless steels industry consistently works to reduce its production CO2 emissions. Industry direct and indirect emissions have, due to solid industry improvement efforts, progressively reduced over the last decade. However, in order to assess the overall emissions picture when using stainless steels and other materials, it is imperative to also determine the emissions throughout a product’s life, i.e.; from ‘cradle to grave’. Only through this approach can a valid materials comparison be made.
By worldstainless
As a starting point and in order to understand emissions associated with the production of stainless steels, it should be noted that within the stainless steels industry there are essentially two active production systems, namely:
- The scrap-based production system in which the bulk of used raw materials are end-of-life stainless steels and/or similar alloy materials that are recycled to produce new stainless steels. This production system is aligned to geographical locations where the availability of end-of-life materials and scrap is high.
- The Nickel Pig Iron (NPI) production system in which the bulk of the Nickel units required for stainless steel production is not derived from stainless steel scrap, but from extracted Nickel ores which are then converted into NPI.
This production system is primarily but not exclusively aligned to geographical locations where the availability of stainless steel scrap is currently low.
There is currently insufficient ‘available-to-use’ end-of-life stainless steel scrap in all regions of the world to permit only a scrap-based production to exist. This situation is likely to remain for the foreseeable future.
To clarify what production emissions exist and where they originate from, and in order to achieve these objectives, we have quantified the CO2 emissions from the three accepted sources.
- Scope 1 Emissions: covering direct emissions from business-owned or business-controlled emission sources.
- Scope 2 Emissions: covering indirect emissions from the generation of purchased electricity, steam, heating and cooling consumed by the reporting company.
- Scope 3 Emissions: associated with the extraction, preparation and transport of ores and the subsequent production and transport of ferro-alloys, including the energy needed for these processes.
These above-described three sources allow us to provide a cradle-to-gate view of the stainless steel industry’s CO2 emissions.
Within the stainless steel industry, scrap has a high intrinsic value. The only limitation is the availability of scrap, especially in developing economies. Furthermore, the long usage life associated with stainless steels restricts the availability of scrap. For example, when stainless steel is used in buildings, it remains in use there for many decades without degradation.
Stainless steels are 100% recyclable and have the highest recycling rate 95%) of any widely used material.
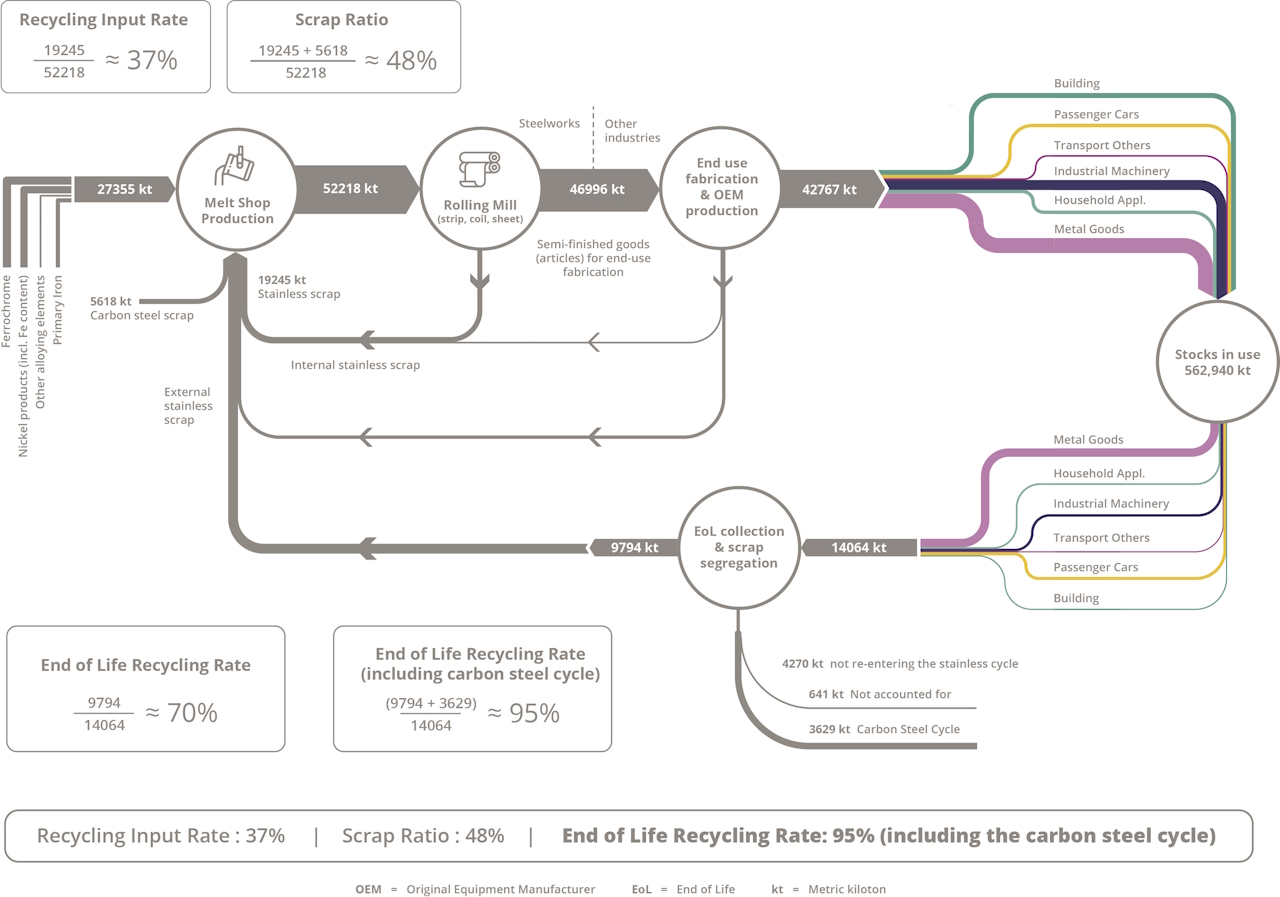
This feature is illustrated in Figure 1, which shows the importance of scrap in the production flow of stainless steel. According to the KIT Stocks and Flows study (2022), 95% of end-of-life stainless steels are collected for recycling. Of the collected end-of-life stainless steels, 74% is directly reused to make new stainless steels and 21% is reused to make new Carbon and Low Alloy steels. At an average global level, almost 50% of the materials used to produce stainless steel are scrap materials, and other raw materials make up around 50% of the material used to produce stainless steel.
CO2 emissions
Recent sustainability studies conducted by worldstainless (between 2007 and 2024) show that emissions from the production and use of stainless steels are generally low. However, and in order to clearly quantify the CO2 emissions during the production of stainless steel, we will identify the CO2 emissions from the categories previously defined as Scope 1, Scope 2 and Scope 3.
• Scope 1 emissions
The current scrap-based producer average is 0.41 tonnes of CO2 per tonne of stainless steel produced. 85%of the producer results sit (normally distributed) in the range 0.20 to 0.50 tonnes of CO2 per tonne of stainless steel produced.
• Scope 2 emissions
The current scrap-based producer average is 0.39 tonnes of CO2 per tonne of stainless steel produced. The figure has dropped from the average figure reported in 2023 which was 0.45. Changes in the regional energy grid mixes have positively impacted Scope 2 emissions, and thereby, the figure has started to become lower than was historically seen.
Scrap proportions |
Tonnes of CO2/tonne of stainless steel |
Scope 3 proportions | |
Scope 1 emissions | 0.41 | ||
Scope 2 emissions | 0.39 | ||
Scope 3 emissions | 85% scrap | 1.15 | 59% |
75% scrap | 1.65 | 67% | |
50% scrap | 2.90 | 78% | |
30% scrap | 6.00 | 88% | |
Total CO2 emissions (ton CO2 / ton stainless steel) |
85% scrap | 1.95 | |
75% scrap | 2.45 | ||
50% scrap | 3.70 | ||
30% scrap | 6.80 | ||
Carbon steel CO2 emissions |
1.89 |
• Scope 3 emissions
Scope 3 emissions cannot be defined in the same manner. There is a linear relationship between the amount of recycled content (scrap stainless steel and scrap low alloy steels) charged and the magnitude of Scope 3 emissions. The higher the recycled content, the lower the Scope 3 emissions. Furthermore, the available data only covers recycled content (also known as the scrap mix) between 40%scrap and 97% scrap, which yields the following Scope 3 emission levels.
- 50% scrap; 2.90 tonnes of CO2 per tonne of stainless steel produced
- 75% scrap; 1.65 tonnes of CO2 per tonne of stainless steel produced
- 85% scrap; 1.15 tonnes of CO2 per tonne of stainless steel produced
NPI production currently produces emissions in the average range (designated by geographical source) of 60 to 85 tonnes of CO2 per tonne of Nickel produced. This means that if NPI is used to make an 8% Nickel containing stainless steel, the increase in Scope 3 emissions (when compared to a 40% scrap mix) associated with this route will typically be between 4.0 and 6.0 tonnes of CO2 per tonne of stainless steel produced.
NB: for comparative purposes, a 40% scrap mix with zero NPI delivers a Scope 3 emissions level of 2.80 tonnes of CO2 per tonne of stainless steel produced.
Life cycle emissions
As stainless steels are reusable, durable, and corrosion resistant materials offering low maintenance needs and a long service lives it is important to consider life cycle emissions, ie; all the Carbon-equivalent emissions released during the different phases of the product life cycle. It is also needed to determine the emissions frequency at each stage over the life cycle, covering material production, material transport, material fabrication, fabricated product transport, installation, maintenance, replacement, and recycling.
Material life cycle emissions
Figure 3 below shows the CO2 production and maintenance emissions for stainless steels, carbon steel and aluminium. Two different stainless steels have been included, namely Stainless 1 which is produced with an 80% recycle content and Stainless 2 which is produced with a 60% recycled content.
The data comprises CO2 tonnes emitted per tonne of material produced plus any CO2 emissions associated with regular maintenance needs. The Carbon steel emissions increase every 10 years due to regular maintenance needed to supress corrosion. Stainless Steels and Aluminium emissions do not increase as their passive films prevent the need for regular maintenance.
The CO2 emissions data and associated included recycling credits are industry supplied figures. The Aluminium data has been adjusted downwards to reflect the fact that the density of Aluminium is about one third that of carbon steel and stainless steels.
Example: the life cycle of water bottles
It is possible to illustrate how stainless steels can, in the long term, be the material offering the lowest CO2 emissions. The life cycle emissions of two reusable water bottles are shown below. The Stainless Steel water bottle has higher CO2 production emissions, but because this bottle will last at least 20 years and a PET* bottle will need to be replaced at least 10 times in these 20 years, the stainless steel water bottle will ultimately be the lowest emitter of CO2.
Summary
It is fair to say that considering production, emissions for stainless steels are only partly informative. There are two high-level production systems at play, both of which are necessary to support the global demand for stainless steels. Over the coming years, the production emissions associated with Nickel Pig Iron (NPI) will progressively fall as greener technologies for the production of NPI become widely adopted. Furthermore, the life cycle emissions associated with using stainless steels offer a different and more compelling perspective for the benefits of using sustainable and resilient materials. Selecting materials that do not degrade and equally do not require significant maintenance and/or partial replacement presents a different and much lower emissions profile.
Need more information?
More information on application-aligned comparative materials sustainability modelling can be found via info@worldstainless.org or on the worldstainless website:
https://www.worldstainless.org/about-stainless/environment/stainless-steels-and-co2-industry-emissions-and-related-data/
About this Tech Article
Appearing in the December 2024 issue of Stainless Steel World Magazine, this technical article is just one of many insightful articles we publish. Subscribe today to receive 10 issues a year, available monthly in print and digital formats. – SUBSCRIPTIONS TO OUR DIGITAL VERSION ARE NOW FREE.
Every week we share a new technical articles with our Stainless Steel community. Join us and let’s share your technical articles on Stainless Steel World online and in print.