The production of sigma and chi phases in cast and wrought super duplex stainless steel at temperatures ranging from 700 to 1000° C has been widely studied. However, to date, research has not examined the impact of particle size or interphase distance on the percentage of precipitations. A team at the University of Padua set out to close this research gap.
By Saira Sehar, Mirko Pigato, Claudio Gennari & Irene Calliari, University of Padua, Italy
Stainless steels were developed during the first decades of the twentieth century in the United Kingdom and Germany. There are four primary types of stainless steel: duplex (high corrosion resistance and strength), martensite (high strength), ferrite (high temperature strength), and austenite (high corrosion resistance). Because of their superior mechanical qualities and resistance to corrosion, stainless steels are alloys that find extensive applications in several industrial sectors.

Duplex stainless steels (DSSs) are a class of steels with austenite and ferrite as the two main phases. Combining different phase-stabilizing components of both phases yields the austenite and ferrite phase assemblage. In order to offer enhanced resilience against pitting and crevice corrosion, DSS is combined with several elements, including Cr, Mo, N, W, and Cu. (1). The PREN categorizes DSS into four grades: lean, standard, super, and hyper. In an environment containing chloride, PREN is a numerical measure of resistance to pitting corrosion; the higher the number, the higher the resistance to pitting corrosion. A PREN of 32 or higher indicates that the material is resistant to pitting corrosion in seawater; super duplex stainless steel (SDSS) has a PREN of 40 or higher. SDSS is appropriate for applications involving seawater desalination and offshore plants because of its corrosion resistant qualities. (2)
These DSS grades are susceptible to the production of harmful complex phases during thermal ageing, such as chi (χ), sigma (σ), secondary austenite, and/or chromium nitrides, due to their high alloy content. At temperatures of 600–1000°C, the ferritic phase is extremely unstable and can break down into secondary phases. Phase transformations are vital to the functioning of SDSS, including the creation of χ, σ, and other secondary phases (3,4). Previous research (5) has demonstrated that intermetallic secondary phases are harmful to the mechanical and corrosion-resistant qualities of steels. Because sigma can create a substantial amount (up to roughly 30 vol pct) in DSS, it is the most harmful. For this reason, understanding the kinetics of sigma-phase development is crucial for managing mechanical qualities and corrosion.
Given the variations in the nominal compositions and microstructures of the cast and wrought alloys, it is expected that the phase transition kinetics and even phase equilibria will change. The production of sigma and chi phases in cast and wrought super duplex stainless steel was widely studied at temperatures ranging from 700 to 1000° C. Higher sigma phase was observed at 900°C for a long duration. Grain size or interphase distance significantly impacts the percentage of secondary phases that precipitate. However, prior research has not examined the impact of particle size or interphase distance on the percentage of precipitations. (6) Thus, this research gap will be filled by our current investigation. Our present study will contribute to demonstrating the comparison of Phase transformation in Super duplex stainless steel in cast and wrought conditions at different temperatures, soaking times and interphase distances. (3)
Table 1: Nominal Composition of Cast SDSS
Elements | Cr | C | Fe | Mo | Si | W | Cu | Ni | N | Mo | P | S |
%Comp (wt) | 24-26 | 0.03 | Bal | 3-4 | 1.0 | 0.50-1.0 | 0.50-1.0 | 6.5-8.5 | 0.20-0.30 | 1.0 | 0.030 | 0.001 |
Material & method
This investigation focused on cast material (UNS S32760, ASTM A890/6A); its chemical composition is shown in Table 1. Compared to other duplex grades, it contains copper and tungsten, which enable them to endure more harsh conditions. The starting material (designated as received, or AR) consisted of ingots of cylindrical specimens.
Wrought SDSS UNS S32760 SDSS plate, commercially known as Zeron 100, has a slightly different composition than cast SDSS. The samples are already in a solubilized condition (at 1100°C for 2h) to have an almost equal duplex microstructure to avoid precipitation of secondary phases and achieve a nearly equal ratio of austenitic and ferritic phases.
Experiment and results
The isothermal ageing treatments were carried out at 850, 900, and 950°C for times ranging from 3 to 90 minutes, followed by water quenching. The volume fraction of ferritic phases in the solubilized etched sample was quantified using ImageJ software. The average area fraction of ferritic (phase δ) was quantified at 54% and the remaining 46% was austenitic (phase γ) without any secondary phase in the cast SDSS; wrought SDSS has 58% δ phase and 42% for the austenitic phase.
Ferrite is enriched with chromium and molybdenum, which are known to promote intermetallic phase formation. These microstructural changes can occur during isothermal ageing, welding, or cooling after solution treatment. They are mainly concerned with the a-ferrite as the alloying diffusion rates are about a hundredfold higher in this phase than in the austenite.
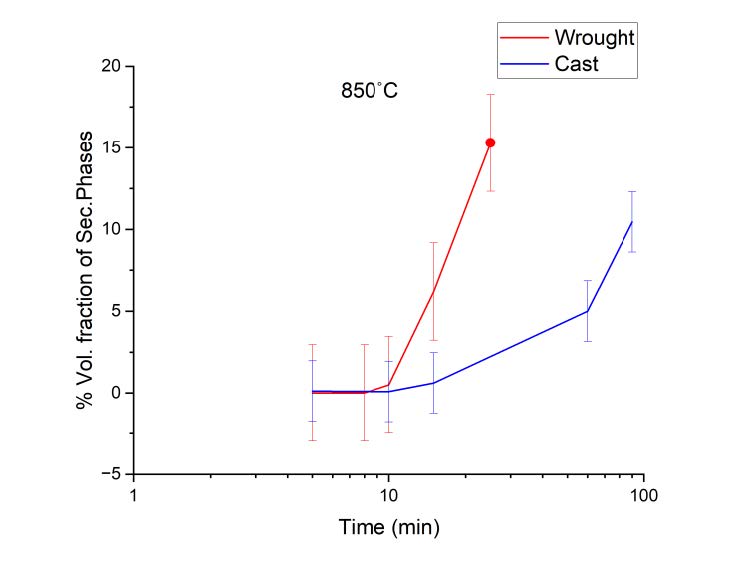
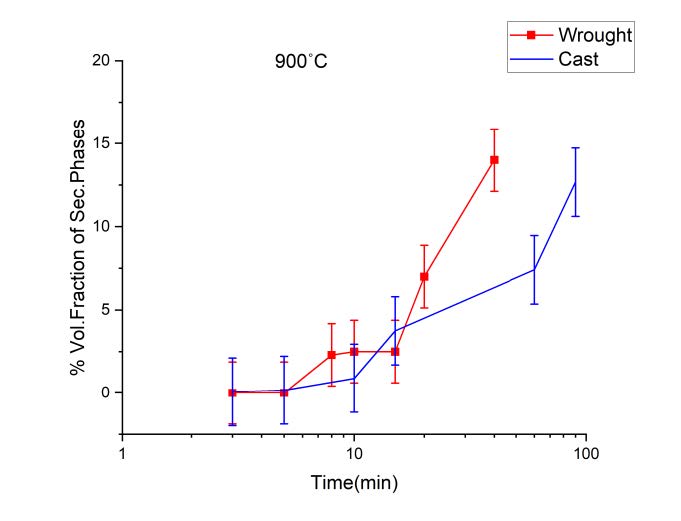
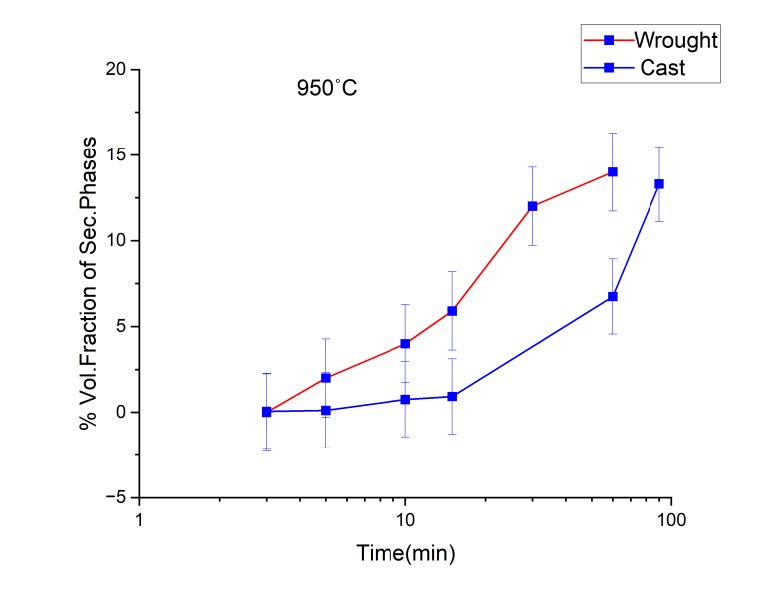
Isothermal heat treatment
Both σ-phase and χ-phase start their nucleation process soon after the initial ageing treatment and after the precipitation of nitrides (in between 3 minutes). When the ageing duration increases, these phases are randomly distributed on the grain boundaries and within the grains (from 15 minutes onwards).
In the cast sample at 850°C, at 3 min chi was the only phase to appear. After increasing the ageing time to 15 min sigma phase starts to nucleate from the chi phase at the ferrite and austenite phase boundary. At 60- 90 min, both phases nucleated at the grain boundary or within the ferritic grains up to 7.92%. For wrought SDSS, at 3 min and 5 min no phase was detected. However, at 10 min <1% and for 15 min 6.2% and a maximum of 15%, both phases were detected at 25 min.
In the cast sample at 900°C, from 3 to 10 min of ageing >1% of both phases appear at the grain boundary. As ageing time increased to 60-90 min, both phases nucleated at the grain boundary and within the grain up to 12.67%. The rate of precipitation of sigma increased after 15 minutes while the rate of chi phase was lower. For wrought SDSS, χ phase appeared after 5 min at the grain boundaries with some isolated ϭ phase particles. A significant increase in χ amount was detected after 10 min; χ particles are coarser and more numerous, while the ϭ content is quite constant, with a moderate size coarsening. After 40 min, χ, ϭ and nitrides are present.
χ phase is always at the boundary’s ferrite/austenite and ferrite/ ferrite. The ϭ phase penetrates in the ferrite or grows along the austenite/ferrite boundaries. The ferrite decomposition is not completed. The rate of ϭ precipitation increases after 20 min, while the χ rate is lower.
At 950°C in the cast sample at 3 min, chi phase appears but when the ageing time is increased to 15 min, sigma phase starts nucleation from chi phase at the grain boundary. After 15 min sigma phase is not only on the grain boundary but also within the ferritic grains. At 60 min, a maximum of chi phase is converted to sigma phase and some nitrides are present inside the chi phase. At 90 min, no chi phase is detected, which indicates that chi phase keeps good stability until 900°C temperature, which is in agreement with our observation. A maximum of 13 % of sigma phase formed at 90 min. For wrought SDSS, at 950°C the first precipitates of χ appear after 3 min, generally decorating the grain boundaries and a few inside the ferrite grains, while ϭ appears after 5 min. The fraction of ϭ phase increases with time, while that of the χ phase decreases after 30 min. At 60 min, no chi phase and a maximum 14% of sigma phase appear at this time.
* Average distance of χ/δ interfaces, Calculate with Interceptions Method
No | Material | Condition | % Sec Phases at 850°C for 10 min | *Average interphase distance (μm) |
1 | UNS S32760 (ASTM A890) | Cast | 0.5-1 | 45 |
2 | Zeron 100 SDSS | Wrought | 5-6 | 33 |
Comparison of interphase distance
Grain size or interphase distance significantly impacts the percentage of secondary phases that precipitate (7), as described previously. The interphase distance of our findings was compared with previous findings that concluded that with larger interphase distance, less secondary phases formed, while with less distance more precipitations are observed. In our finding, double interphase distance was found to have significantly less sigma and chi phases.
Conclusions
- During the ageing treatments, the χ phase is the first intermetallic phase that precipitates, always at the α/γ boundaries and at the triple points; it is followed by the σ phase that gradually becomes embedded and eventually replaces the former.
- Cast SSDSS showed less precipitation as compared to wrought SDSS. Wrought SDSS has less interphase distance compared to cast SDSS.
References
- Kim YJ, Chumbley LS, Gleeson B. Continuous Cooling Transformation in Cast Duplex Stainless Steels CD3MN and CD3MWCuN. J Mater Eng Perform. 2008 Apr;17(2):234–9.
- Michalska J, Sozan´ska M. Qualitative and quantitative analysis of σ and χ phases in 2205 duplex stainless steel. Mater Charact. 2006 Jun;56(4–5):355–62.
- Calliari I, Breda M, Ramous E, Brunelli K, Pizzo M, Menapace C. Impact Toughness of an Isothermally Treated Zeron®100 SDSS. J Mater Eng Perform. 2012 Oct;21(10):2117–23.
- Acuna A, Riffel KC, Ramirez A. Sigma phase kinetics in DSS filler metals: A comparison of sigma phase formation in the as-welded microstructure of super duplex stainless steel and hyper duplex stainless steel. Mater Charact. 2024 Jan;207:113433.
- Angelini E, De Benedetti B, Rosalbino F. Microstructural evolution and localized corrosion resistance of an aged superduplex stainless steel. Corros Sci. 2004 Jun;46(6):1351–67.
Other references can be provided on demand.
About the author
Saira Sehar is a PhD Student in Material Engineering Department of University of Padua, Italy. Her main focus is on phase transformations in SDSS through isothermal heat treatment in cast and wrought SDSS and their effects on Mechanical and Electrochemical properties of SDSS. She will start working on Additively Manufactured SDSS to compare it with cast and wrought SDSS.
Email: saira.sehar@studenti.unipd.it
About this Tech Article
Appearing in the December 2024 issue of Stainless Steel World Magazine, this technical article is just one of many insightful articles we publish. Subscribe today to receive 10 issues a year, available monthly in print and digital formats. – SUBSCRIPTIONS TO OUR DIGITAL VERSION ARE NOW FREE.
Every week we share a new technical articles with our Stainless Steel community. Join us and let’s share your technical articles on Stainless Steel World online and in print.