A sample of Hybrid Steel on high temperature tensile test.
In 2017, Ovako introduced a step-change in the evolution of steel metallurgy with the launch of Hybrid Steel. The aim was to challenge the long-established divisions between the specific steel categories of tool steel, maraging steel, and stainless steel, merging their unique properties into one high-performance steel grade with the production economy of conventional engineering steel. This invention was enabled by professional alloying and a successful combination of alloy carbide and intermetallic precipitation hardening.
By Dr Steve Ooi, Ovako, Dr Cem Örnek, Leibniz Institute for Materials Engineering and Istanbul Technical University
Hybrid Steel offers superior strength over conventional steels, especially for high temperature applications. It has a particular appeal for use in engine components, bearings and tools that operate in extreme environments and in demanding conditions. Due to its high hardenability, Hybrid Steel does not need to be quenched to achieve a fully martensitic structure for the subsequence tempering process. This results in minimum component distortion and enables a reduction in final machining processes. Furthermore, Hybrid Steel has remarkable corrosion and oxidation resistance. Even with a much lower chromium content, it still has similar corrosion resistance levels as the lower end of stainless steels. This exceptional corrosion resistance can be attributed to the balanced presence of alloying elements, including nickel, molybdenum, aluminum, and chromium. These elements, in their proportionate amounts, collectively form a mixed oxide layer that exhibits a synergistic effect. This means that when one type of oxide layer faces deterioration, the others continue to support the overall structural integrity, contributing to the material’s outstanding corrosion resistance in acidic and chloride-bearing solutions. The aim of this recent research was to gain a deeper insight into the corrosion performance of Hybrid Steel.
Stainless steel relies on a protective native passive film
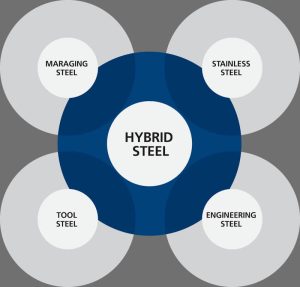
Stainless steel owes its exceptional corrosion resistance to its protective passive film that forms spontaneously on the surface. The native passive film of most standard stainless steel is a hydrated chromium-rich oxide or oxyhydroxide in the form of Cr2O3·Cr(OH)3 and iron oxyhydroxide species with a thickness of about 2 nm, with temperature having an impact on composition and thickness. The surface oxide has no fixed composition and structure; there is a gradual change in composition across the thickness and lateral space, and it keeps changing in composition and structure over the degradation time. In varying oxidation states, other elements, such as molybdenum, silicon, and nitrogen, can also participate in oxide or hydroxide formation, depending on the alloying elements and their concentration. Previous projects using calculation of phase diagram (CalPhaD)-based thermochemical calculations have shown that nickel cannot form the native passive film of 25Cr-7Ni super duplex stainless steel, and the composition is a spinel-mixed type of oxide, primarily FeCr2O4. These calculations agree with our synchrotron X-ray analyses. However, bivalent nickel oxide/oxyhydroxide can be formed when the steel is anodically polarized. This means that nickel is not a central contributor to stainless steel’s passive film. However, it has been demonstrated that the enrichment of nickel beneath the oxide, known as the surface alloy layer, provides a barrier to the dissolution kinetics, resulting in increased corrosion resistance.
Typically, stainless steel requires a chromium concentration of at least 10.5% by weight that must be homogeneously dispersed within the iron alloy. This threshold is due to the percolation network of chromium atoms forming a continuous bond with oxygen along the entire surface. Chromium is a more active element than iron and can create a highly dense and capacitive oxide. Although the dielectric constant of iron oxides is higher than that of chromium oxide, charge transport through chromium oxide is far more sluggish due to more effective compactness and lower defect density.
Therefore, the corrosion resistance of stainless steel increases with the chromium concentration. However, most engineering steel used in the industry is protected against corrosion by extrinsic means, such as coatings, inhibitors or cathodic protection. This is because cost factors limit the use of highly-alloyed stainless steel.
Test program
The aim of this project was to understand why Hybrid Steel, with a concentration of 5% Cr, exhibits corrosion resistance remarkably similar to 14% Cr-containing stainless steel. This comparison aimed to shed light on the underlying mechanisms through two primary experimental approaches: (1) analyzing the passivation behavior in sulfuric acid solutions, including the impact of anodic polarization on passivity disruption, and (2) examining the corrosion dynamics in near-neutral chloride-containing solutions to confirm the presence of spontaneous passivity and its vulnerability to pitting. Subsequently, the structure and composition of the surface oxide layer were scrutinized using Hard X-ray Photoelectron Spectroscopy (HAXPES) to identify the factors contributing to Hybrid Steel’s exceptional corrosion resistance.
This work was further augmented by thermochemical modeling, enhancing our understanding of the phenomenological occurrence in materials science history. The tests were carried out on Hybrid Steel 55 in both the as-rolled condition, with a hardness of 35 HRC and tempered to increase the hardness to 55 HRC.
Test results – the beneficial effect of aluminum
The electrochemical measurements showed that the Hybrid Steel has similar corrosion behavior to grade 420 martensitic stainless steel in de-aerated sulfuric acid and near-neutral sodium chloride solutions. Hybrid Steel exhibits spontaneous passivity, remarkably low anodic current densities in the microamperes range, and resistance to pitting corrosion, indicative of characteristics akin to stainless steel.
Nevertheless, Hybrid Steel, with merely 5% Cr, challenges this notion, suggesting that chromium oxide’s role in its passivity cannot be the sole explanation. Indeed, while the 10.5% Cr threshold holds for pure iron-chromium alloy systems, Hybrid Steel’s composition includes additional elements, such as aluminum and molybdenum, that also play significant roles in enhancing its passive behavior. The CalPhaD-thermochemical computation analyses, augmented by the HAXPES results, showed that other alloying elements participate in the surface oxides, supporting chromium oxide in corrosion protection. This indicates that the surface oxide is predominantly composed of Fe2O3 · FeCr2O4 · NiO · AI2O3, which changes structure, fraction and existence over electrochemical polarization.
Furthermore, the thermochemical modelling shows that when Cr(VI) species form upon transpassive breakdown of Cr2O3, the interfacial pH is reduced, which causes some dissolution of the remaining passive surface oxides. Therefore, Hybrid Steel could repassivate despite the loss of Cr2O3. In addition, the computational calculations and HAXPES analyses have shown that Al, Ni and Mo oxides exist beyond the polarization at electrochemical potentials above the transpassive dissolution potential of chromia.
The clear conclusion is that oxides other than chromium oxide contribute to the passivation of Hybrid Steel. It exhibits superior extended passivation capabilities, outshining traditional stainless steel’s corrosion resistance, which primarily relies on chromium oxide for protection. In this context, aluminum oxide is highly beneficial. Aluminum oxide forms a dense, potent, sluggish oxide to electron transfer reactions. Hybrid Steel exhibits passive behavior in both heat-treated conditions, as apparent from its polarization behavior in acid and chloride solutions. It is worth highlighting the role of nickel in the surface oxide which also supports the passivity of Hybrid Steel. Nickel usually does not form an oxide due to its sluggish kinetics to oxidation as compared to iron and chromium. Therefore, nickel does usually not participate in the native passive film of stainless steel, not even in nickel superalloys. However, remarkably, nickel contributes to the surface oxide and thereby improves the surface nobility of Hybrid Steel.
Particular emphasis on the contribution to passivity must be given to aluminum. It provides continuous support to the mixed-type surface oxide, explaining the passive nature of the steel. Our work indicates that the synergy between the mixed oxides provides exceptional passive behavior.
A new potential for designing sustainable stainless steel?
Hybrid Steel has not been developed for use in acidic environments. We conducted this test program to characterize and understand the passive layer nature of Hybrid Steel. The conclusion is that it offers exceptional corrosion resistance that allows a comparison to low-alloyed stainless steel.
Sustainable materials must be corrosion-resistant at affordable costs. Whether or not Hybrid Steel can be declared as a stainless steel or possibly a corrosion-resistant steel, tomorrow’s stainless steel will be manufactured with precise alloying of elements contributing to passivity. Regarding the corrosion-resistance-to-cost ratio, the suggestion is that a mixed noble oxide with a similar metal cation fraction may outperform a passive with chromium oxide only.
Ultimately, the work suggests that steel can be made stainless-like with a diligent alloying recipe without requiring the conventional Cr threshold concentration of 10.5%.
About the authors
Dr Steve Ooi is Group Technical Specialist with Ovako, based at Cambridge University. His work specializes in alloy and process design in the context of steels for complex engineering applications where component failure can lead to major consequences. Much of his research has therefore been focused on critical components in aeroengines, automobiles, stress-cancelling welding alloys, deep-ocean structures and bearings.
Dr. Cem Örnek is head of the Surface Technology Department at the Leibniz Institute for Materials Engineering, and concurrently holds a position as an adjunct professor in the Department of Metallurgical and Materials Engineering at Istanbul Technical University. His research is dedicated to the comprehensive understanding of material degradation phenomena, encompassing areas such as corrosion and wear.
Reference
“Understanding the passive behaviour of low-chromium high-strength Hybrid steel in corrosive environments”: https://www.nature.com/articles/s41529-023-00392-z
About this Featured Story
This Featured Story appeared in Stainless Steel World March 2024 magazine. To read many more articles like these on an (almost) monthly basis, subscribe to our magazine (available in print and digital format) – SUBSCRIPTIONS TO OUR DIGITAL VERSION ARE NOW FREE.
Every week we share a new Featured Story with our Stainless Steel community. Join us and let’s share your Featured Story on Stainless Steel World online and in print.