Solid-state hydrogen storage systems based on metallic materials which chemically absorb large amounts of hydrogen under moderate pressure and temperature and then release them back when heated have niche applications in the emerging hydrogen economy as part of the decarbonized world.1 They can help form very compact and reversible hydrogen storage devices which are also capable of delivering hydrogen at high pressure on demand via heating.
By Rupsha Bhattacharyyaa,b, Rami S. El-Emamc,d and Farrukh Khalide
At one point of time, solid-state hydrogen storage systems were in serious consideration for hydrogen-based vehicles where on-board hydrogen storage had to be very compact due to space limitations, though current attention has shifted to high-pressure gas storage in polymeric composite vessels. Given that there are hundreds of such materials developed and tested by various research groups and a handful of them are also commercially available now, it is important that a simple quantitative material selection framework is available to potential users who are looking to develop and utilize these systems for specific applications. This article discusses one such method developed recently by the authors2, which makes use of thermodynamic properties of the hydrogen storage alloy, the engineering design considerations and energy management requirements during the hydrogen storage and retrieval phases to enable material selection for a given application.
Working principle

The underlying principle of using reversible hydride-forming alloys for gas compression and delivery is schematically illustrated in Fig. 1 which is a temperature-pressure curve for any generic alloy. At temperature T1, the alloy absorbs hydrogen and gets saturated with it along the nearly horizontal line between the points marked 1 and 2 at constant source pressure P12 while releasing the heat of hydriding reaction in the exothermic process. When heat at temperature T2 is provided to the saturated alloy it begins to release hydrogen at the higher pressure P34 and the alloy’s condition shifts from saturated with hydrogen at point 4 to nearly hydrogen-free at point 3. Thus, a gas storage-compression-release cycle is completed by operating the system at two temperature levels, without needing any turbomachinery for gas handling. This allows for some simplification of operation in small-scale systems where trained operators may not always be available.
Guidance framework for material selection
Different materials for solid-state hydrogen storage have different pressure-temperature characteristics and hydrogen storage capacities as described previously. That means that for a given delivery pressure, materials have to be heated to a different temperature. This makes the engineering design of each such system unique and therefore it has to be customised for a given application. For example, if a material has to be heated beyond 450–500°C to get the desired final pressure, a regular steel tank will not be suitable for housing the alloy, and more exotic metallurgy such as Hastelloy may have to be considered. In the same way, different alloys release different amounts of heat when absorbing hydrogen (i.e., different heat of reaction or ΔH values in the last column of Table 1), thus different kinds of cooling may be required for systems based on them. Finally, material costs and availability are additional considerations for system design. A step-by-step approach is shown in Fig. 2 which uses alloy-specific data and simple design calculations that enable a user to identify the good, if not the best candidate materials for their specific application. It also assigns weightage factors to the various criteria (identified as wi in Equation 1 below), to give different levels of importance to the criteria. It is therefore a ranking scheme that makes use of multiple aspects of a hydrogen storage material instead of solely focusing on the storage capacity and presents an integrated metric (called CM or Combined Metric) that quantifies all these dimensions and builds them into the decision-making or selection process.
The value of CM for any of the alloys designated as alloy i is calculated following the steps in Fig. 1 and finally by using equation 1. Each factor is compared to the largest value of the same factor for all the alloys considered to normalise the value. CM lies between zero and one, and the lower the value of CM, the better is the alloy for a given set of wi values. This therefore becomes the alloy selection criterion under this framework. The values of w1 to w5 can have any values between zero and one. Some examples are shown in Table 2. The sum of w1 to w5 must be equal to one in each case.

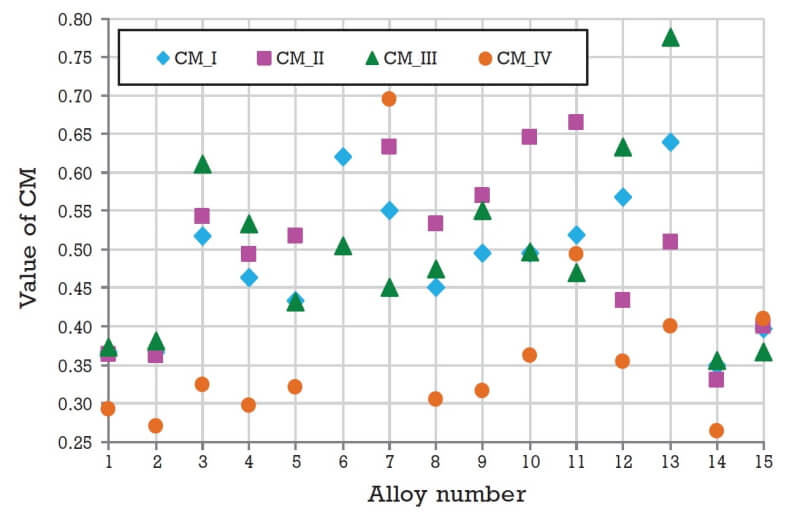
Application of the guidance framework – a case study
The case study for analysis and utilization of the framework described earlier is taken as the replacement of a high-pressure hydrogen gas cylinder, which is typically found in laboratories or shop floors, by a metal-hydride-based system which can store an equivalent amount of gas and can deliver it at pressures up to 150 bar. Fifteen commercially available metal hydride-forming alloys are considered as the options available to design the system for such an application.3 The equilibrium temperature needed for each alloy to decompose to a pressure of 150 bar is different. This temperature must therefore be used to set the design temperature for each tank. The total quantity of gas is taken as 300 mol for the purpose of calculations, since this is what is found in typical commercial cylinders.

Results and analysis
The results of the calculations performed as per Fig. 2 are shown in Fig. 3. Using the calculated value of CM, one can easily determine that for the specific example considered here, Alloy 14 has comparatively the best performance out of all fifteen alloys considered, irrespective of the selection criteria set or weightage factors used to evaluate it. All other alloys have CM values greater than that for Alloy 14. Hence this material can be taken as a good starting point for designing a metal-hydride-based hydrogen storage and compression system. All available materials can be ranked using the value of CM and in case the best identified material is not available, the second ranked material can be chosen.
Conclusions
Choosing a suitable material for a given solid-state hydrogen storage and recovery application can be very application specific since no material possesses all the desirable characteristics for all kinds of end users. Thus, having a simple yet rational evaluation scheme is helpful for system developers. One such scheme is illustrated in this article that makes use of available data about potential hydrogen storage alloys and calculates an integrated, weighted average metric that accounts for various features and enables logical comparison of the options. The calculations are simple enough to be implemented on a spreadsheet-based system as it makes use of limited data and straightforward equation-based calculations only.
Author affiliations
a Applied Systems Analysis, Homi Bhabha National Institute, Mumbai, India
b Heavy Water Division, Bhabha Atomic Research Centre, Mumbai, India
c Faculty of Engineering and Applied Science, Ontario Tech University, Oshawa, Ontario, Canada
d Faculty of Engineering, Mansoura University, Mansoura, Egypt
e Department of Mechanical Engineering, Istinye University, Topkapi Kampüsü, Teyyareci Sami, Sk. No. 3, 34010, Zeytinburnu, Istanbul, Turkey.
Re-published with kind permission from Hydrogen Tech World.
References
- Bellosta von Colbe, J., Ares, J., Barale, J., Baricco, M., Buckley, C., Capurso, G., et al. (2019). Application of hydrides in hydrogen storage and compression: Achievements, outlook and perspectives. International Journal of Hydrogen Energy, 44(15), 7780–7808. https://doi.org/10.1016/j.ijhydene.2019.01.104
- Bhattacharyya, R., El-Emam, R. S., & Khalid, F. (2022). Multi-criteria analysis for screening of reversible metal hydrides in hydrogen gas storage and high pressure delivery applications. International Journal of Hydrogen Energy. https://doi.org/10.1016/j.ijhydene.2021.12.168
- da Rosa, A. (2005). Fundamentals of Renewable Energy Processes (1st ed.). Academic Press.